While the operator stays safe, indoor drones carrying lidar and SLAM technology create a 3D map of the inside of hazardous spaces
Nuclear power plants, ballast tanks, underground mines, toxic chemical plants, sewers, offshore oil storage, decommissioned industrial facilities—none of these are places suitable for humans; yet monitoring and inspection of the interiors are often required to check for defects or damage. Advanced collision-tolerant drones that carry lidar and other sensors provide a better way to view and map dangerous indoor areas.
Send in the Drone
Drones are successfully being used to monitor and inspect bridges, dams, utility poles, and other hard-to-reach places, with some manufacturers receiving approval for flying beyond visual line of sight (BVLOS) and conducting continuous autonomous monitoring. However, operating in GNSS-deprived confined spaces poses a different challenge.
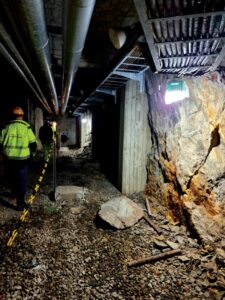
A decommissioned power plant has “no-go” zones that contain potential hazards, making them difficult to map. Photo credit: Flyability.
Ideally, data is collected without putting the operator into a hazardous situation, but without visual line of sight, the pilot cannot know exactly where the drone is in a tunnel, pipeline, or storage tank. It is difficult to ensure the entire interior is recorded, and if a problem is detected, only the approximate location is identified.
To address the GNSS issue, the Flyability’s Elios 3 drone uses visual sensors and a lidar sensor to stabilize and locate itself in space. The lidar data also allows it to produce real-time 3D maps with FlyAware, a Simultaneous Localization and Mapping (SLAM) engine, which shows the pilot its location. The 3D model viewed on a tablet in real time helps locate the drone in space, even with low visibility due to dust or poor lighting. After the flight, a survey-grade 3D map using lidar data is created with 3D modeling software.
Elios 3 collects video and takes still pictures at the tap of a button to capture flaws, cracks, or holes and records the geolocation of any point of interest. The inspection data is localized by producing an accurate trajectory with a sparse point cloud offering a good balance between accuracy and processing time. Afterward, a video player supports reviewing and visualizing the data frame-by-frame to bookmark points of interest, and Flyability’s Inspector software documents, classifies, and measures the problem areas for reporting purposes.
“3D models of any hard-to-reach indoor space can be used as a record for changes over time that indicate flaws or defects, and an as-built of the interior is useful for conducting safe repairs or demolition,” says Zacc Dukowitz, senior communications manager at Flyability. “GeoSLAM 3D modeling software creates a 3D model from the lidar data, which provides meaning and context, as well as a high degree of accuracy. Compared to visual inspection or data collection with stationary devices or in person, the drone is faster and safer.”
In addition to being protected by a collision-resistant cage, the Elios 3 uses patented technology to flip right-side up in case of an accident. It also carries a thermal camera, and it is designed to carry a second sensor to allow inspectors to collect other types of data. Possible sensors that Flyability may choose to incorporate with the Elios 3 may read radiation or gas levels or even test ultrasonic thickness.
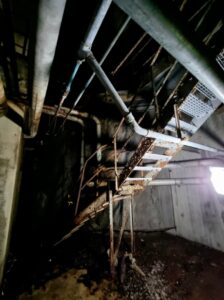
Mapping the 130-foot-tall staircase using ropes and scaffolding would have been dangerous and time consuming. Photo credit: Flyability.
Into the “No-Go” Zone
A large power company in Europe that owns and maintains complex infrastructure in several countries was already a Flyability customer when its personnel learned about the Elios 3. As a “proof of concept” for more extensive use of autonomous drones to map places that were too dangerous for people to enter, the utility tested the Elios 3 inside a decommissioned power plant that has been closed for decades, specifically to map a multi-story staircase designated as a “no-go” zone.
“Without the Elios 3, they would have used traditional methods to map the staircase, involving ropes, possibly scaffolding, and specially trained personnel,” said Dukowitz. “It would have taken three to four days to plan and carry out the data collection, while the drone was finished in 30 minutes, without needing to send people into the danger zone.”
To map the entire area, the drone had to fly about 30 meters to 40 meters (98 feet to 130 feet) up the stairwell, demonstrating its ability to operate a long distance from the pilot while maintaining a strong signal.
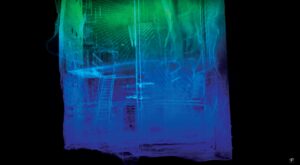
The operator viewed a real-time 3D model as Elios 3 flew up the staircase of a decommissioned power plant. Photo credit: Flyability.
“The results of this project indicate that the Elios 3 is effective for inspecting and mapping complex industrial infrastructure, making the process much safer, faster, and less expensive,” Dukowitz said. “The SLAM-generated models and the post-processed 3D models provide all the materials needed to support decommissioning and maintenance efforts.”
Growth Areas
Any industry with large assets that require regular inspections, such as mining, water/sewer/wastewater infrastructure, oil and gas, maritime, pharmaceutical and chemical plants, and power generation, could benefit from indoor drones. Given the environmental challenges and limitations on entering these structures, companies often have limited knowledge of their layout, which can impede their ability to safely manage and maintain their assets.
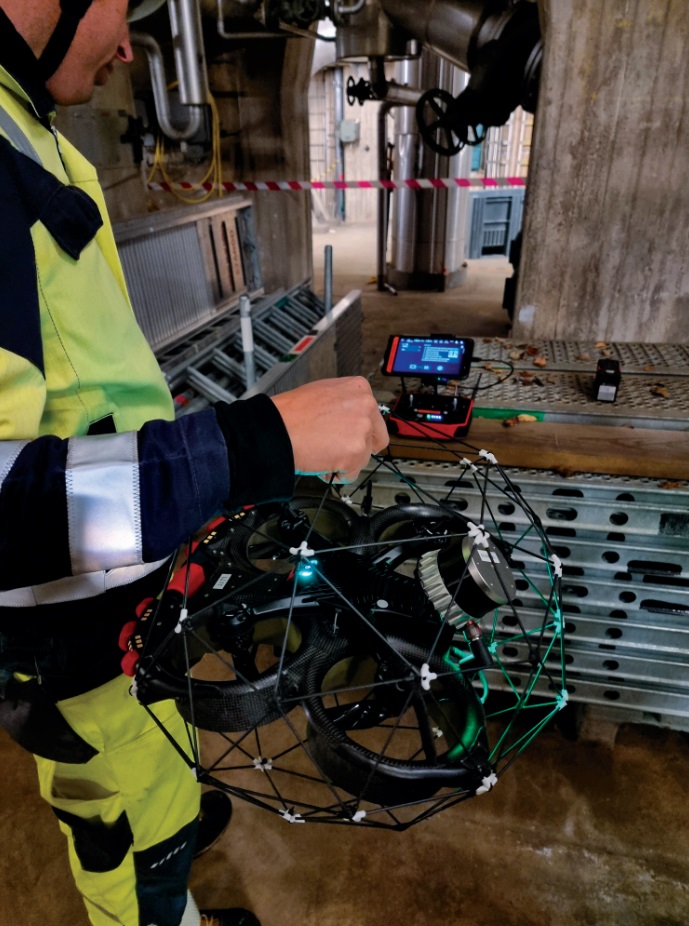
The collision-resistant Elios 3 drone flies using visual sensors and a lidar sensor to stabilize and locate itself in space. Photo credit: Flyability.
Due to the potential danger of radiation from nuclear energy generation, nuclear power plants are ideal candidates for remote mapping to comply with government requirements. One relevant regulatory mandate is ALARA, which stands for “as low as reasonably achievable,” and requires radiation exposure be limited as much as possible for personnel, within budgetary constraints and technology. Flyability equipped the Elios 2 RAD drone with a radiation sensor specifically to map radiation levels without exposing workers to danger.
“Over 80 percent of U.S. nuclear operators already use Flyability’s indoor drones for their visual inspections,” said Dukowitz. “The ability to produce survey-grade maps of sensitive areas without exposing inspectors to radiation makes indoor drones a very attractive option.”
The Elios 3 is designed to be customized for the specific demands of users by attaching different payloads for each application, and it is equipped to operate in conditions not suitable for humans. Lidar and SLAM technology combine to make the inspection and monitoring process safer, faster, and more efficient by providing real-time visibility, as well as comprehensive 3D maps.