A discourse on UAV lidar from the perspectives of a vendor and a user.
IS A UAV LIDAR SYSTEM REALISTIC?
While UAV lidar is definitely a breakthrough for vendors and users alike, is it enough? Can UAV photogrammetry deliver what is really needed by the surveyor and engineer?
Indeed it can, but only in part. If the mapping area is solely hard surfaces (dirt and pavement) then photogrammetry is a viable solution.
Of course, most of the world is covered by vegetation, ranging from short grasses to shrubs and large forests. In these areas the automatic, small-format photogrammetry solution cannot penetrate to an approximate ground surface that is needed for engineering purposes. Here enters lidar.
In the late 1990s, lidar was widely adopted by almost all larger photogrammetry firms. It was (and still is) rather expensive (often more than $1 million), but it allowed for huge areas to be collected much more quickly and accurately than with conventional photogrammetry and a team of stereocompilers.
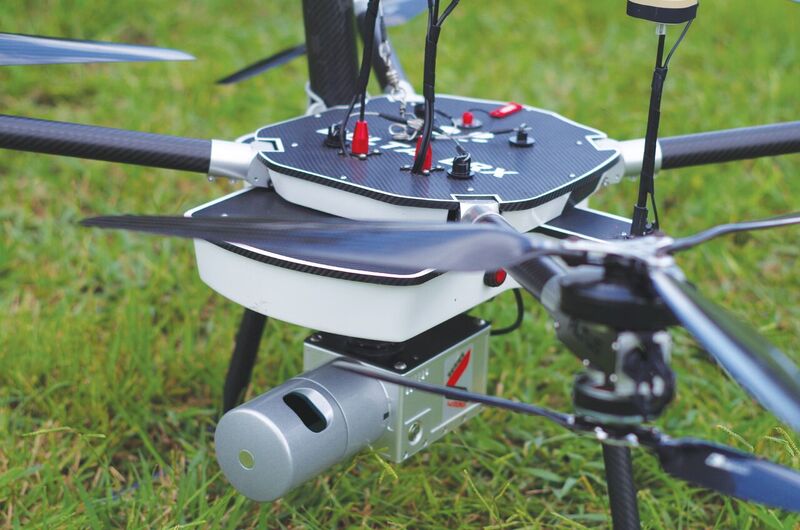
An Altus LRX multicopter outfitted with a Snoopy A-series HDL-32E.
With such expensive systems, where does that leave us with UAVs? Can lidar be used on a UAV just as photogrammetry is being used? A lot of literature promotes the idea that UAVs and lidar just don’t mix or that lidar is too expensive, too heavy, etc.
While UAV lidar is more expensive than most UAV photogrammetry systems, UAVs make a good platform from which you can de- ploy a lightweight, yet highly functional and affordable lidar system. What is true is that until just recently UAV mapping, both with imaging and with lidar, was not practical largely due to FAA restrictions. Fortunately, the 107 regulations have mitigated this problem.
RANGE
What is necessary to make UAV lidar a practicality? First, a lightweight laser scanner with enough range to make it usable. At a minimum this translates to a flying height of about 45 to 50 meters.
Ideally, we’d like to reach the 400-foot ceiling to maximize our efforts. This translates to at least 150-meter laser range. The choice of sensor in this case is dictated by the user’s business model, as a larger range is often more expensive.
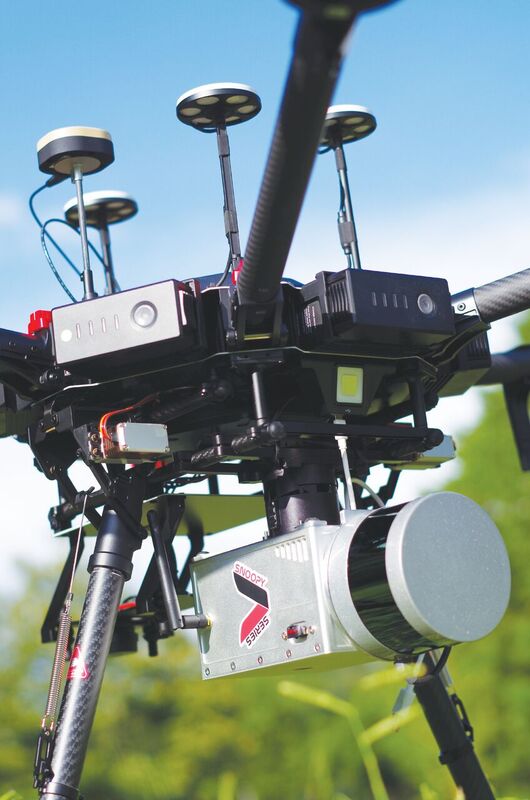
A DJI Matrice 600 Pro UAV with a Snoopy A-series and a Velodyne Puck.
INS
The INS (inertial navigation system) is like the central nervous system of the lidar system. The INS has to be good enough, or it doesn’t matter how good the laser is. This means the orientation must be able to provide a sufficient angular result (much like a theodolite or total station for surveying), or the solution is of little value.
Of course, the GNSS receiver must also be able to provide sufficient positioning accuracy. Usually this means an L1L2 PPK solution. The INS must also be small, compact, light, and affordable.
There are several systems that currently meet these requirements, and virtually all of them are MEMS-based. The FOG systems generally provide more performance but at a significant cost and weight increase. In addition, with the 400-ft ceiling they offer little improvement to the end product.
EXTRAS
The scanner and the INS are the main two components, but to this we have to add additional electronics, a lot of R&D, and a super healthy dose of software, both for the PPK solution and point-cloud generation. With the right recipe, we can find lidar systems that weigh from 1 to 6 kg. In general, the heavier the system, the longer the range, the bigger the UAV required, and the more expensive the system.
COST AND WEIGHT
The cost and weight of the lidar system drives the next decision: What UAV do you use? A multicopter with three, four, six, eight, or more motors? Fixed wing? Helicopter? Gas or electric?
How about portability: size and power? Does a huge case matter or is a backpack necessary? Do you always drive to your jobs? If yes, then battery size and case size rarely matter.
If you fly to the site on commercial airlines, then size and batteries have to be carefully considered. The heavier systems will definitely require shipping the UAV and batteries ahead of time, usually by ground or water transport. That alone can be expensive (in lost time for transit).
WHICH SYSTEM IS RIGHT?
Designing a UAV lidar for surveyors and engi- neers requires factoring in all of these considerations. It is no small undertaking to build a UAV lidar system, but make no mistake about it: these systems exist and are working hard every day, delivering what the surveyor and engineer needs to get the job done.
These systems range in price from around $40,000 to over $400,000. The system that is right for you depends upon your clientele, environment, and resources. A $40k system can do a lot of work, but don’t make it compete against a $400k system. Likewise, a $400k system can do a lot, but sometimes the $40k system is by far the better choice for the job.
If your business does a lot of topo work using traditional surveying instrumentation on 10- to 1,000-acre tracts, then a $40k to $120k lidar system may be the perfect solution. The difference would then be in the UAV.
A $10k or less UAV may be perfect for the business that scans only 5 to 10 flights per week, but somebody scanning more frequently or in more harsh conditions may require a $40+k UAV built for industrial use.
Again, the lidar and the UAV need to be matched to the business. There is no one-size-fits-all option.
SCAN TO DELIVERABLE
The following are details from a company that uses lidar with their UAS for surveying. Established in 1950, C. H. Fenstermaker & Associates is a multi-disciplinary consulting firm based in Louisiana that specializes in engineering, survey and mapping, environmental consulting, and advanced technologies. Fenstermaker uses UAVs both with photographic and lidar sensors; however, given the environment along the Gulf Coast, lidar has advantages there.
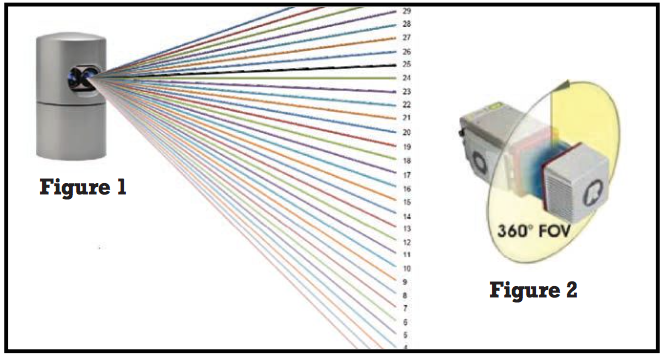
Figure 1 & Figure 2
CHOOSING THE RIGHT SENSOR
Only a few years ago, the option for airborne lidar as UAV payload was reserved for large, expensive military systems. Today we have a few more options for mobile lidar systems small and light enough to be carried by major-consumer UAV manufacturers.
Given the price point and varied performance on these miniaturized lidar systems, it might be wise to adopt the 75% rule when choosing a sensor. What parameters should one consider when choosing a mobile lidar system, and is accuracy the only thing that matters?
At Fenstermaker, 75% of our survey needs involve areas with some level of vegetative cover with mapping-grade accuracy; with a need for survey-grade accuracy at less than 25% of the time. Of the dominant UAV lidar sensors, reported accuracies can range from 1cm on up. The critical element is the ability to penetrate canopy, and therefore a system with more laser channels projected ahead and behind the flight trajectory of the UAV offers the best opportunity to penetrate vegetation and capture bare earth data (Figure 1).
In contrast, the sensor in Figure 2 supports a laser pump and revolving lens (mirror) design, creating a single focused laser channel for improved accuracy.
In consideration, the manufacturers’ reported accuracy of the lidar system is a necessary metric; however, as with low-altitude UAV lidar, point cloud data sets contain numerous points per square inch. This interjects the law of averages to the final result and can diminish the effects of reported accuracies, leveling the playing field to overall accuracy.
FIELD WORKFLOW
Collecting mobile lidar data is relatively easy, but making sure the final product is reliable and accurate requires a few steps in the field to insure a quality deliverable.
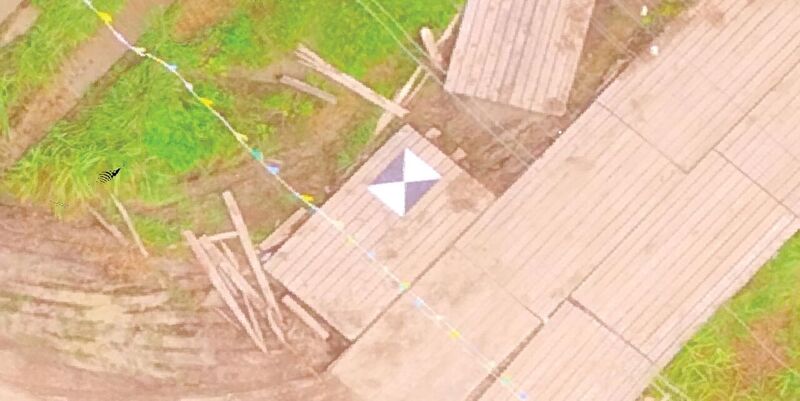
Figure 3
With any aerial data collection, it’s wise to setup control points (Figure 3) or ground check shots to QA/QC the final product. So, what is accuracy? As with most site surveys, consider global and relative accuracy. Global accuracy of the project is in reference to the location of the site globally on Earth, while relative accuracy defines the quality of the measurement between two points within the same data set. Fenstermaker establishes global accuracy by first setting up a site master control point using a local GPS VRS network on state plane coordinates. Transitioning from VRS to base rover (RTK) methods to set remaining site control and ground truth insures maximum relative accuracy.
It is also important to set control and conduct mobile lidar flight within minimal time separation, maximizing relative accuracy while using an overlapping constellation of satelites for the survey session. Typical accuracies using this control strategy range within 0.02’ to 0.07’ and are achievable. Essentially, you are looking at survey-grade results.
OFFICE WORKFLOW
Typically, when speaking of aerial lidar of the past, we might associate deliverables with traditional surface models or Digital Elevation Models (DEM). Today, aerial UAV lidar collected at such low altitudes and relatively slow speeds yields feature-rich point clouds comparable to terrestrial laser scanning. With such data sets, the ability to perform “Virtual Surveying” from the desktop of the point cloud is a reality.
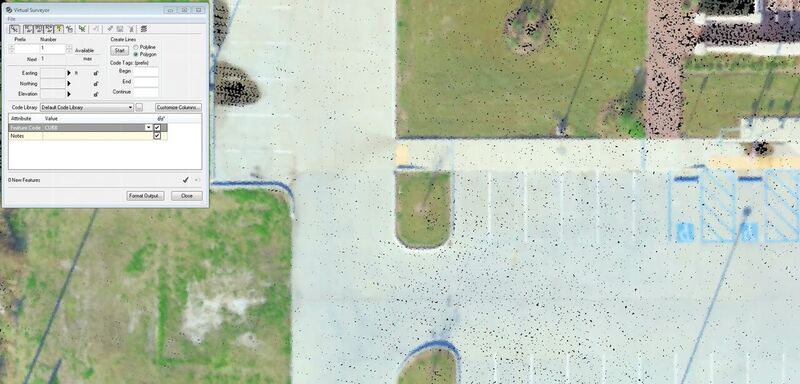
Figure 4
As shown in Figure 4, Fenstermaker uses Cyclone Virtual Surveyor for performing plan- imetric extraction tasks from the point cloud. Following extraction of the planimetrics and cleaning of the point cloud, data is imported into Autodesk Civil 3D for final deliverables.
Fenstermaker has found that, in many cases, the use of mobile UAV lidar can replace or at the very least supplement traditional survey methods for data collection.
To read the rest of the articles in this print issue, click on the issue cover, below.