It’s more about many minor triumphs than major leaps. Surveyors can play an essential role in implementing these changes
To those outside of the industry (and some within), the term “construction automation” evokes visions of bots and autonomous equipment plying construction sites—efficient and tireless—yet always on some far horizon. In present reality, construction automation takes on so many other forms. Automating individual processes may not seem as exciting as bots, but mundane steps can and do deliver substantial cost and time savings.
One can get jaded by the marketing staple of “this is a game changer,” when in reality it is amalgams of multiple, often small, “game changers” that make the difference—a continuum of innovation.
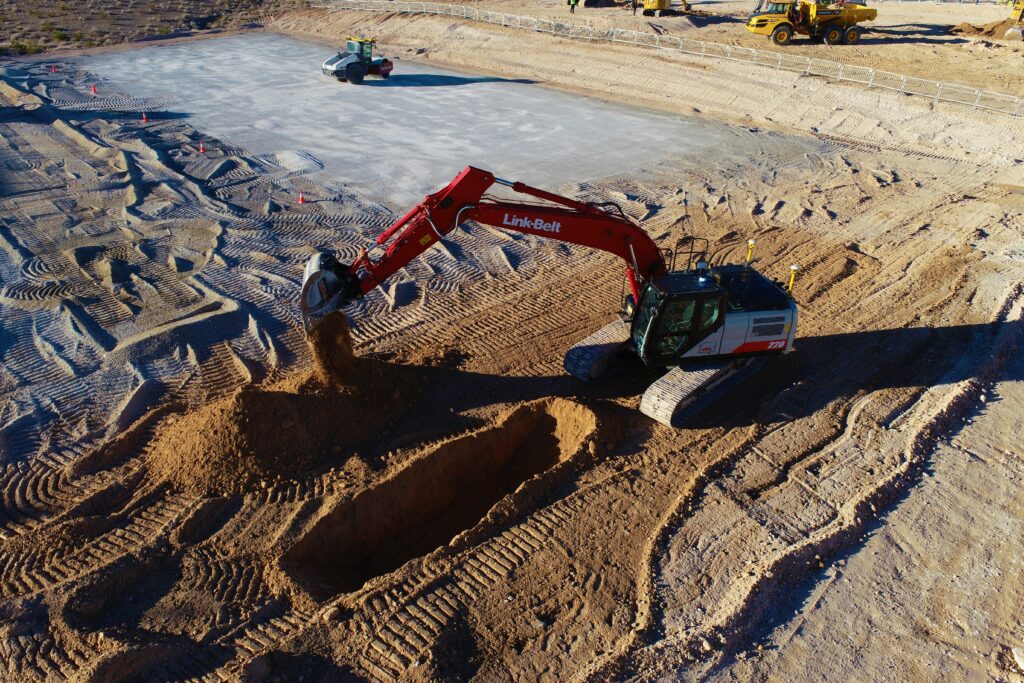
Where’s the operator? Autonomous excavator (foreground) and autonomous compactor (background). Source: Trimble
We’ve seen more focused “small plate” innovation in tools and solutions that contribute to further automation in the past few years than the previous decades put together. Often, these have filled small but problematic gaps in workflows—minor increments that can unleash more substantial change. We can only look at a few in this article and have focused on those that surveyors might have a hand in implementing, or that could affect their work. It seems that whatever construction automation headaches are being experienced, quick searches reveal that there are multiple brands and doses of “aspirin” out there to solve them.
Reducing the Schedule Killers
What can delay or halt production? Logistics problems, process and task coordination issues, safety incidents, compliance, and rework are common culprits. Downtime on a construction site could add up to tens of thousands of dollars lost per day or hour. Many of these issues can be addressed with software solutions that can be integrated into broader workflows, coordinated between work teams, and are increasingly offered as software-as-a-service (SaaS) and in the cloud.
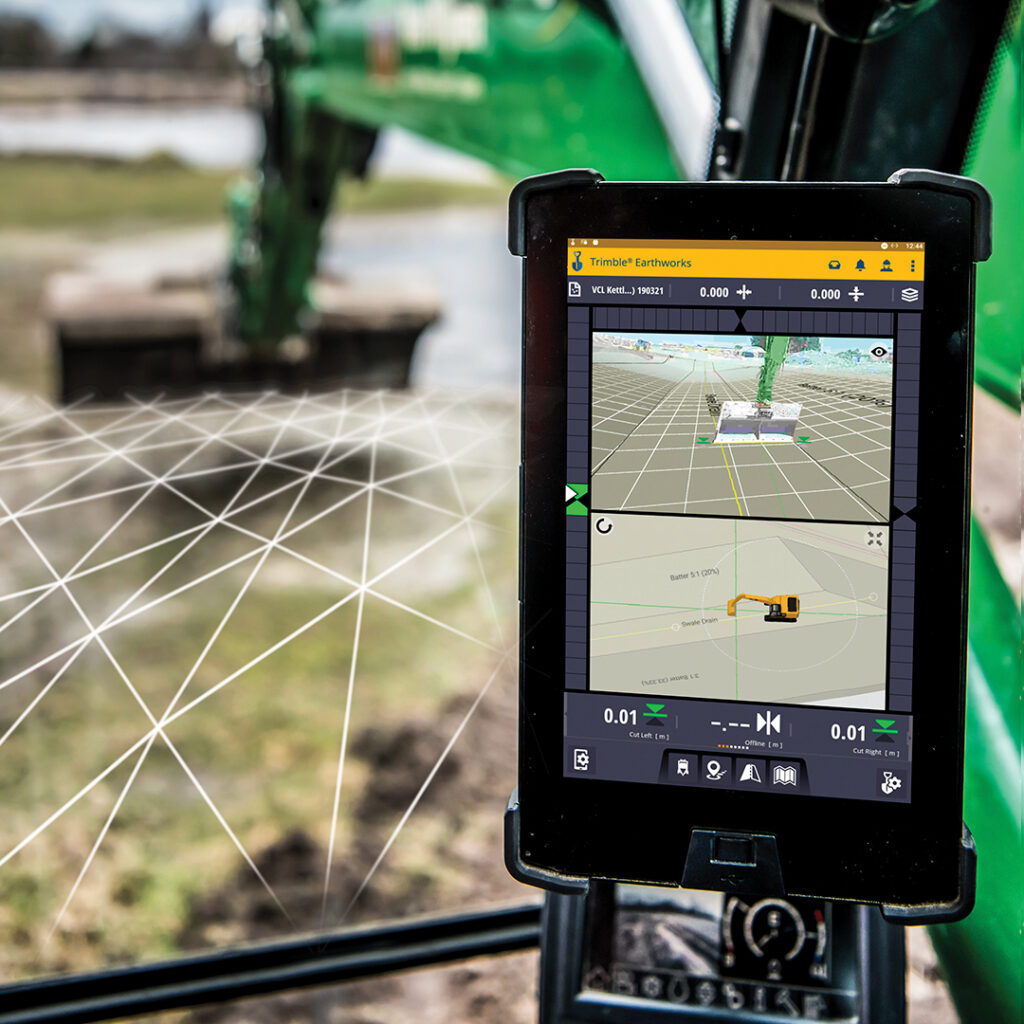
An autonomous excavator following a pre-programed construction plan.
Are the workers on the site authorized for various areas and are their certifications up to date? Site access, workforce management, and compliance should be low-hanging fruit, with so many sensor and software solutions out there.
Situational, proximity, and site awareness through sensors, cameras, and systems can be key for both safety, and site management. Personal beacons for the workforce and moving equipment, plus combinations of lidar, radar, and cameras represent a rapidly growing market.
An example is Georgia Tech’s SiteAware system, which uses a low-power Bluetooth network mesh technology for personal protection units (PPU) that activate hazard alerts based on pre-determined distances: b.gatech.edu/3XCpfd8. There are applications of beacons that also double as low-precision indoor positioning systems, like an ultra-wide-band (UWB) system by Humatics, used for plants, factories, and underground work.
Innovation also addresses is not only worker hearing protection, but also on-site communications. Employing selective noise cancellation, 360 Clear active earpieces can filter out site noise, while allowing close-range voices.
Overall site awareness for workflow management and change detection can be addressed by frequent UAS overflights and mobile mapping, backpack mapping systems, and increasingly with site camera systems. AI can analyze data from these imaging and remote sensing systems for change detection, classification, volumes, and more. An example is Evercam’s 4D View, that integrates Bentley Systems iTwin technology. Site managers can switch between the live views and the project models to track progress and check the fidelity of as-built conditions to the design model.
Addressing Potential Issues in the Design Phase
Key to automation is delivering a detailed 3D design model to the field, like the 3D models loaded into machine control systems. Building to the model, like hitting grade upfront without overcut and undercut, laying out and installing components in the right place, and avoiding clashes; these are prime remedies for avoiding costly (and schedule busting) rework. But what if the model is flawed and you find out too late that it is difficult or impractical to build in the real-world site conditions?
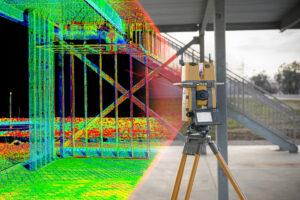
Scanning total stations provide all of the functionality of a high quality robotic total stations for surveying and control work but are also becoming popular in construction for layout and creating instant deliverables for as-built validation. Source: Topcon
Augmented, mixed, and extended reality (AR, MR, and XR) have been adopted not only in the design phase, but also during construction layout. Designers can enhance their field visits with AR, using GNSS to position and orient overlays of 3D design models on sites to see if various design alternatives are a good fit. For example, Norwegian engineering firm ViaNova, discovered a potential problem in a pedestrian bridge design using an AR handheld system: bit.ly/3GNxOL1.
Field AR can come in the form of dedicated and purpose built, integrated systems, or by combining multiple hardware and software elements. One such implementation used a Lecia GeoSystems GNSS smart antenna and correction services, a Zeno handheld field controller, and vGIS software: bit.ly/41qzXWw. Another example of an integrated system is Trimble’s SiteVision, running on a phone or tablet on a purpose-built handle with a Catalyst GNSS system.
Automating Layout
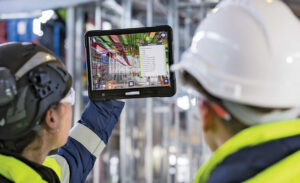
Mixed reality, projecting the 3D design over a live camera view is being used in the design phase, for construction layout, and inspections via field controllers, tablets, and head-up-displays (e.g., HoloLens). Source: Trimble
AR is increasingly being adopted for construction layout. Many surveying/construction field software packages can accommodate import of 3D design models in standard formats like IFC. And the user can see these registered and projected over the view from the instrument camera (e.g. robotic total stations).
The same overlays of 3D design models are being projected in heads-up displays, like with Microsoft’s HoloLens, as adapted in purpose-built versions like Trimble’s XR10 (that fits on a hard hat). The XR10 paired with FieldLink MR software drives a robotic total station, with users choosing the layout points from the model, overlaid on the site view, using hand gestures.
One key limitation of heads-up displays (at this time) is that they are best suited for indoor applications like vertical construction: bit.ly/3GOlNoZ. Field controller and tablet AR can work indoors and well enough in many outdoor conditions.
Construction lasers that have been in use for decades, like the standard spinning lasers, have required major updates. There are now many choices for projecting 3D designs onto the site, especially if indoors.
Projection lasers like those from Faro are in common use. There are even solutions that can create “walkable plans,” projecting a full-scale CAD drawing in an indoor space. Some solutions employ cameras or lidar to get a rough model of the site and can adjust the projections for angled and even curved surfaces.
Bots are making inroads into layout. For indoors, there are multiple bots systems, like HP’s SitePrint, that essentially prints 2D elements of a design on a flat floor surface. For outdoors there are bots, like those from TinyMobileRobots and Civ Robotics, that can do field and road marking. Other bots drill pilot holes for posts, like the Autonomous Precision Survey Rover (APSR) from Terrasmart (for example for solar farms). Others can set stakes, or even set posts and drive piles. Any kind of repetitive task, like large scale layout, is ripe for automation.
There are whole classes of robotic total stations (RTS) that have been purpose designed for construction, paired with software that streamlines the layout process, like several models in the Leica iCON series, or Trimble’s new Ri. RTS can also assist with machine control when conditions for GNSS guidance are not optimal.
The market for such construction RTS, and the potential time/cost saving they represent has spurred R&D into advances in, for instance, improvements for tracking, like the ring-lights added to the scope of the Ri and Hilti PLT series. Whereas historically, advances in RTS were aimed at (no pun intended) mainly surveying markets, it is likely that the next steps in the evolution of RTS will be driven more from the construction side of many manufacturers.
Further, we are now seeing the first tilting prism poles, like Leica’s AP20, that also seeks to reduce sources of error with an automated measure-up feature: bit.ly/3HbgNfw.
Instant Deliverables
Automation in construction, if it is to truly speed processes and avoid delays/stoppage, needs instant feedback. How quickly can construction validation happen after materials are moved, surfaces graded, or components installed? Validation often needs to happen before subsequent tasks can be undertaken.
Beyond UAS flights, site scans, and construction camera solutions already discussed, there are needs for very precise and focused as-built and validation steps. Discrete points taken with optical and GNSS instruments, conventional scans, and photogrammetric techniques often require extra steps, and it may be difficult to validate constriction in the field. New tools and solutions have been developed specifically to overcome these issues.
Construction is benefitting from new workflows that employ, for instance, scanning total stations like the Trimble RX12, Leica MS60, and Topcon GTL-1200. Because these are foremost high-quality total stations, the scan and image sets they also produce can be immediately and precisely constrained to project control.
The points clouds and additional discrete points can be delivered in standard formats without needing additional processing. Or, increasingly, we are seeing application specific workflows that can be performed in the field.
For example, for tunneling, a scanning total station can rapidly produce a point cloud that can be compared in field controller software to identify overbreak and underbreak. For validation of, for instance, structural elements in vertical construction, Topcon’s GTL-1200 has a piggyback scanner mounted above an RTS. The scan can be compared to the design model in ClearEdge 3D.
Project Management and Coordination
Coordinating materials, tasks, schedules, billing, etc., yields substantial cost and time savings. Working in 3D models, BIM, collaboration in the cloud; it would take volumes to go through the (very, very) many backend and connected field software suites that contractors utilize. The key for surveyors is in finding the best way to get data in and out of these environments, and to become adept at working in them.
There has though, been a lot of work toward closing some gaps between the design environments and model-based construction. It can be cumbersome to seamlessly transition from what had traditionally been 2D design environments to full-on 3D models.
For instance, Bentley Systems announced in November of 2020 that it has added functionality in its MicroStation and OpenRoads design platforms to better interface with its iTwin environments. This kind of development will eventually be something seen in field software: being able to create/update elements of collaborative models that automated construction will need more of.
Machine Control: The March Toward Autonomy
When it comes to machine control it is more about the journey than the destination. The general consensus in the industry is that widespread autonomy in heavy civil equipment may still be on a far horizon. However, construction becomes more efficient with every step taken to get there.
The spectrum of automation in machine control could be viewed as four levels. The first is indication. The equipment knows where it is, typically via GNSS or RTS, and the operator sees this on the design model, and guides the equipment and operates the implements, like the blade or bucket—essentially assisted guidance.
The next level is implement control. While precision agriculture implementation may control many types of implements attached or towed by the equipment, in construction this is typically a blade or bucket. In addition to the GNSS, there are sensors on blades or articulations in a boom and bucket that show where those are in relation to the model, to help guide the operator to meet the design.
The next level is automatics—automated steering, boom hydraulics (increasingly fly-by-wire systems), and bucket control (even for rotating buckets). The driver initiates movements with the stick, but the equipment and implements will move on their own to meet the design model.
One step in advancing automatics to autonomy is simply adding speed control. But the bigger hurdle is the feedback systems and electronic brains needed onboard to set a piece of equipment on its course to meet the design model without being a hazard on the site.
While much of the R&D for vehicular autonomy can help boost implementation for construction, in many ways it is much more complex. Autonomous cars use feedback systems like radar, lidar, and cameras to simply avoid hitting things in its way. Construction needs to push, excavate, or otherwise form things. And in some cases, for safety or other reasons, there may still be a desire to have a person in the cab.
Long before autonomy is a widespread reality, automatics will likely grow as it becomes harder to fill the demand for operators with decades of experience.
But there is one key thing that all of these automation processes have in common; they need 3D models. And who better to create these, or update the digital twins of construction sites? Surveyors. Construction automation may change the way things are done, but surveyors can, and have been, adapting.
Sidebar:
When to Automate?
While there has been a boom in new and upgrade infrastructure construction across many regions of the globe, construction as an industry continues to suffer from, to varying degrees, narrow margins. And with this comes aversion to the risks of implementing hardware and process automation. This has only been exacerbated by recent trends.
A report outlined in the October 2022 edition of The Civil Quarterly (by Dodge Data and Analytics, produced in partnership with Infotech and Hexagon) reveals that while contractors continue to expect an increase in revenue and profit margins, it is notably less than the previous quarter. Potentially this could be due to acute supply chain issues and the specter of a potential economic downturn. Oddly, this comes at a time when the ratio of contractor’s current level of backlog and the level they consider ideal is at 97 percent, which suggests they are already near capacity in their volume of work. Furthermore, 77 percent report very high confidence in the volume of work expected in the near future.
Contractors we’ve spoken to seem to be split on the subject of further automating during these times of increased contract opportunities. Some say they are too busy to stop and upgrade, while others indicate that further automation is the only way they can take on more contracts.
Perhaps the transition to a more automated construction site is best served by the incremental nature of industry related innovation. There have though been convergences of new tech and process upgrades that are yielding substantive gains not possible even a few years ago. Ironically, the pandemic years spurred more design and construction firms to modernize in the areas of process, project management, and collaborative platforms. And the uptick in projects has driven more equipment operators to step up to higher levels of equipment automation.