Milestone advances since the early days got scanning to where it is now
This is my final article in the series. 3D scanning has come incredibly far since I joined start-up Cyra Technologies back in 1998. There have been many advances over the years. In this article, I discuss what I think have been its biggest milestone advances and my take on each of them.
Hardware/Scanners
Overall, advances in 3D scanners have dramatically improved the technology’s productivity, affordability, and ROI. It’s hard to pick milestone advances that I think have been the most significant, but here goes.
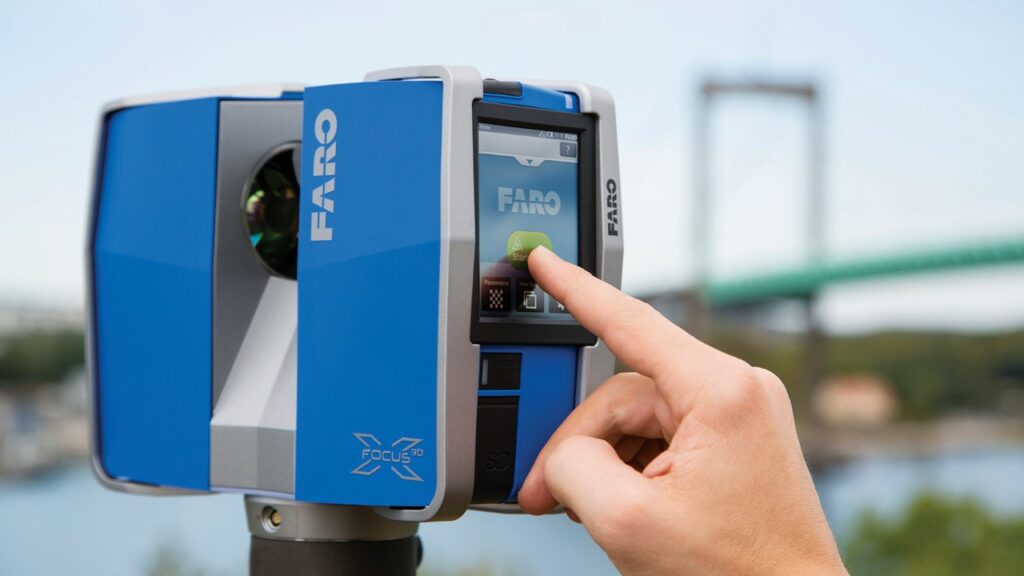
2010 was a big year for scanner milestones. The Leica ScanStation C10 (left top), introduced April 2010, and the Faro Focus3D (above), introduced at the end of 2010, were the first scanners to feature onboard controls and batteries. The Leica C10 also had survey-grade, dual-axis tilt compensation which enabled survey traverse-based registration. The Focus3D scanner was also a huge advance for scanner size, weight, ease-of-use, and piece point. Also released in 2010, Optech’s Lynx Mobile Mapper M1 (left bottom) brought mobile mapping scanning to the market. Credits: Leica Geosystems, Faro, Optech
Survey-grade Tilt Compensation – This feature (standard in total stations) first showed up in a laser scanner in the Leica ScanStation in 2006. It enabled better registration and geo-referencing—a huge boon for surveyors—and it remains a highly valued feature.
Onboard Controls & Batteries – All first-generation and many next-generation laser scanners were controlled with a laptop, and many had external batteries. That was OK, but they were a logistical hassle on site.
Released in April 2010, the Leica ScanStation C10 brought the first fully contained scanner to the market. It was followed later that year by Faro’s Focus3D scanner. In both systems, scanner control and batteries were contained in the laser scanner unit itself—a huge boost in logistical convenience. Both the C10 and Focus3D were released during a major economic recession, yet both products were extremely successful in the market.
Smaller, Easier-to-use, More Affordable – Faro broke the mold with their Focus3D scanner back in late 2010. It was less than half the size, weight, and price of any other laser scanner at the time, plus its simple onboard controls made it easy for non-surveyors or non-engineers to use. Its availability also brought in many new types of users. Years later—in 2017—the Leica BLK360 set a major, new level of small size and weight, simplicity, and price point.
Mobile – “2D or Profiling Scanners” have been around before 3D scanners, used as profiling instruments for tunnels. However, the first mobile laser scanning system that drew big-market interest was Optech’s announcement in 2010 of its Lynx Mobile Mapper M1, typically mounted atop a van. Mobile scanning has grown dramatically since then.
Mobile scanning gives up accuracy compared to tripod-based systems, but its field productivity gains over static scanning—often 10 times—and its “accurate enough” capabilities for many applications represent a huge advance. From van-mounted scanners to pushcart scanners and backpack scanners, and now to affordable SLAM-based hand-held scanners, mobile scanning is booming. The use of lidar on drones is yet another mobile example.
Scanning and Imaging Speed – At the end of the year 2000, the industry’s most popular scanner—the Cyrax 2500—scanned at 1,000 points per second. Scan times of 15 minutes to one hour per scan were common for all early scanners. Riegl later innovated the ability to add true color digital imagery by mounting a digital camera atop the scanner, but adding true color was time-consuming. All that has improved dramatically.
Scan speed specs rose to more than 500,000 points per second via the 2003 introduction of Z+F IMAGER 5003.
Cameras within a scanner now take digital imagery blazingly fast. In addition to faster digital imagery, the quality of digital imagery applied to
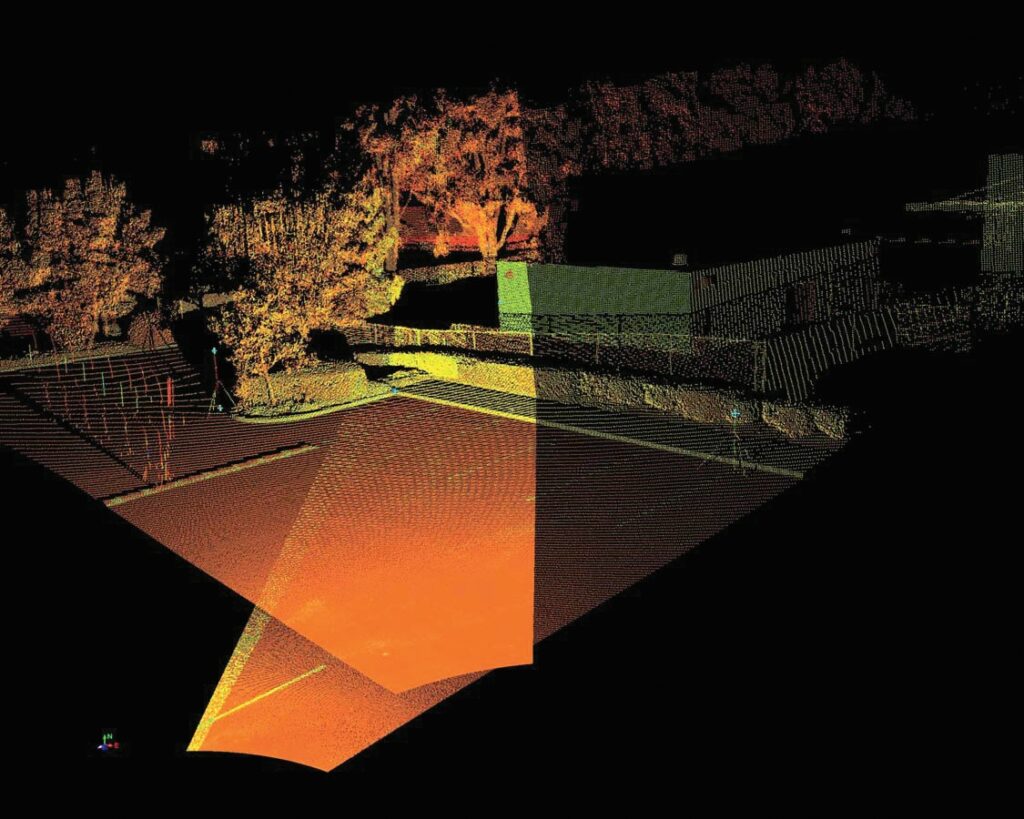
Leica Cyclone 4.0 introduced “cloud-to-cloud” registration capability—the ability to register point clouds without using targets—in 2002. Credit: Leica Geosystems
scan data has also dramatically improved. Times per scan, complete with high-quality image capture, are now down in the one- to five-minute range per scan and image capture.
Register-as-you-scan – Technically, this capability was introduced in 2006 with the first Leica ScanStation that had a built-in, survey-grade dual-axis compensator. But that capability didn’t become efficient until years later as Leica, Riegl, and later, Z+F developed better workflows and instrument capabilities for doing this time-saving task.
Point Cloud Software
Many software advances over the years have been made to keep up with advances in scanners. Others have offered important, new deliverables and big, new productivity and versatility benefits. Here are ones that I see as major milestone advances.
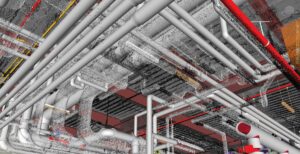
With the introduction of the EdgeEise software in 2009, ClearEdge3D innovated automated point cloud modeling, in this image for piping. Credit: ClearEdge3D
360-degree Panoramas on the Internet – The earliest 360-panoramic images, with distance measuring and mark-up capability, arrived via Leica’s TruView software (2006) and CSA’s PanoMap application (roughly same time period). For the first time, this software made it easy to view and measure from 3D scans in a totally intuitive way—even on the Internet—and to “hop around” a scanned site. Prior to this, users had to be skilled in 3D to extract value from point clouds—a big barrier to adoption.
Point Cloud Capability within CAD – Another big, early barrier to adoption for 3D scanning was its unfamiliar software user interface. Users could only work with point clouds in dedicated point cloud software, such as Cyra/Leica’s CGP/Cyclone or Mensi’s 3Dipsos software. Those interfaces were totally different from CAD and mapping software interfaces to which users were accustomed.
The first software that enabled users to extract value and create deliverables from point clouds within a familiar CAD interface were point cloud plug-ins. Many CAD users simply used point clouds as a
background reference for design.
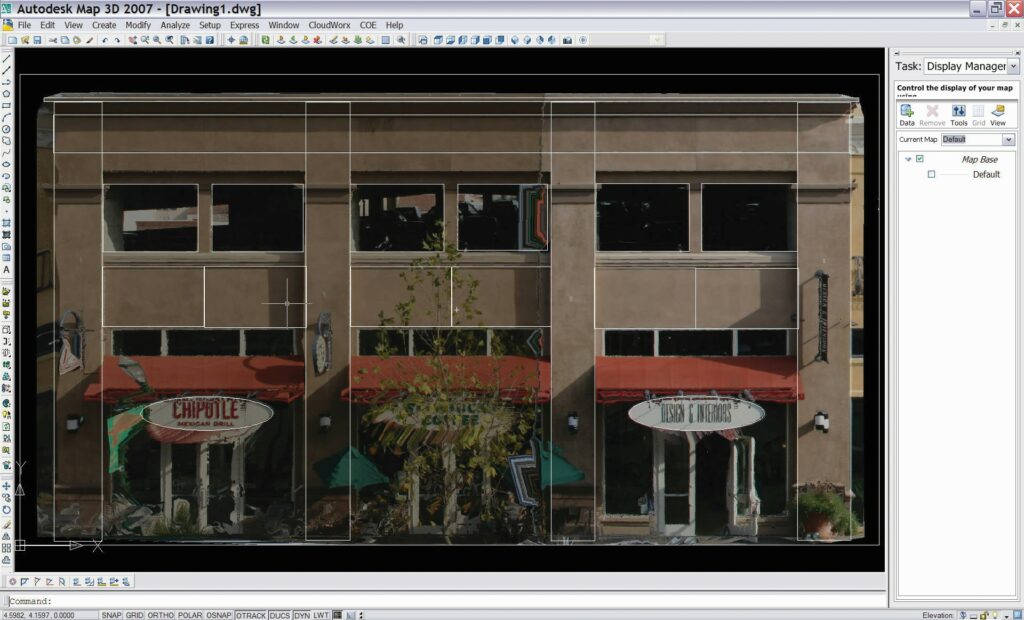
The ability to produce orthoimages from point clouds for immediate export to CAD was a big, time saving advance. Credit: AutoDesk
Additional plug-in features provided helpful capabilities for working with large point cloud files. The first plug-ins came from BitWyse (2001, LaserGen for MicroStation), Leica (2001, CloudWorx for AutoCAD and MicroStation), and Kubit (early 2000s, Pointsense for AutoCAD). In 2006 Trimble acquired BitWyse and in 2015 Faro acquired Kubit.
Many years after the arrival of point cloud plug-ins, CAD vendors started adding respectable point cloud capabilities to their own software, but plug-ins remain popular thanks to their extra features and better performance with large files.
Large File Handling – This has been a steady-but-crucial area of improvement for working with point clouds. As scanner speeds increased, users often scanned more densely and performed more scans. Vehicle and airborne mobile scanning took those file sizes even further. The net result was a steady, dramatic increase in point cloud file size.
Advances in computers, graphics cards, IT infrastructure, etc. relieved part of the burden of working with large point cloud files, but key advances in point cloud software itself have also helped greatly.
Of those advances, one milestone that stands out was the introduction of Euclideon point cloud software in 2013. It allowed fast streaming of even the largest point cloud files sets and sharing files without having to copy them. Doing these types of tasks today using cloud services has been another major advance.
Cloud-to-cloud Registration – In the early days of 3D scanning, registration was only done using targets (or by modeling specific objects) in overlapping scans or simply visually (which was very difficult). Placing targets (and surveying targets) in good locations for registration not only took extra time in the field, but in many cases site logistics made it difficult or impractical.
In 2002, Leica introduced “cloud-to-cloud” registration in a new standalone Cyclone REGISTER module. This breakthrough enabled users to register overlapping scans—without using targets—by aligning scans to each other simply based on overlap scan geometry. This field-efficient technique is widely used today, although supplementing with targets is also often recommended for highest accuracy registration. Targets are also needed for proper georeferencing.
There have been numerous other advances in registration processes that have greatly reduced the time in the office needed to perform registration. Today, this step takes a small fraction of the time it used to take.
More Workflows & Types of Deliverables – In the early days of 3D scanning, there was basically one workflow. You imported scans into your point cloud software, registered them, and then processed or modeled them into objects (e.g., planes, cylinders, meshes, lines, etc.) one at a time for export to CAD or mapping software. Once in CAD, those objects would be incorporated into creating final as-built or mapping deliverables. That was it. It was tedious and time consuming.
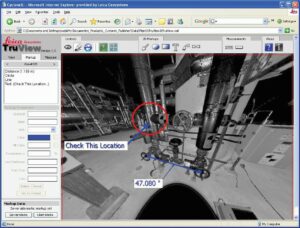
Introduced in 2006, Leica TruView brought intuitive 360-degree panoramic images, with measurement and markup capability, to the market. Credit: JJH
Then, along came a rash of valuable new workflows and deliverables. One of the earliest was an ability to bring CAD objects such as piping designs into point cloud software and perform 3D pipe routing and clash analysis directly within point clouds, a huge time saver over modeling point clouds into 3D as-builts for export to CAD. Another major workflow advance was the introduction of “Virtual Surveying” to create topographic maps. With this workflow, a user could create linework and feature code scan points directly in point cloud software for ready export to mapping software. Point cloud meshing tools have become dramatically more efficient over time and the ability to quickly spit out orthoimages directly from registered scans has proven both beneficial and popular.
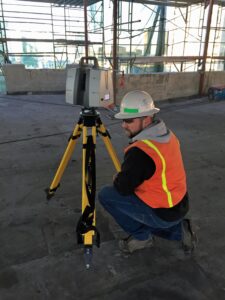
In the early days of 3D scanning, virtually no one had ever heard of BIM. Today the use of laser scanning in construction on BIM projects may be its largest use. Image courtesy: Rick Engineering
As noted above, the ability to create 360-degree panoramic images, with strikingly true color, was a huge advance in deliverables. Yet another major advance was simply the ability to provide registered point clouds as a standalone deliverable—unheard of in the early days. In my start-up days at Cyra Technologies, CEO Ben Kacyra used to preach a vision of point clouds being a “new currency” in the AEC world. He was right.
Automated Point Cloud modeling – Early-on, the Holy Grail for processing point clouds into models was to do it with a single click—fully automated. A huge challenge for this vision is that scanning captures everything, not just the specific objects that need to be mapped or modeled.
It’s a daunting task to account for “everything” and achieve one-click, fully-automated modeling. Despite this, there have been some major advances in this space, most notably the 2009 arrival of EdgeWise software by ClearEdge3D (Topcon acquired ClearEdge3D in 2018), the first software to automatically model certain points within point clouds into groups of objects. Improvements in this type of software over time—as well as an expanded roster of objects that can be automatically modeled—have made it a good choice for many projects.
Major New Markets/Applications
In the early days, 3D scanning was used successfully for industrial plant as-builts, civil infrastructure mapping of bridges and busy roadways, mining and tunneling projects, and heritage documentation. However, it was not cost-effective for many applications it’s used for today. As the technology became more efficient and accepted, some major new markets and applications opened up for it. Here’s my take on what those major new markets and applications were.
Forensics – The potential to use laser scanning to accurately capture a crime scene or a forensic incident was apparent early on. For example, it was used to capture damage done to the USS Cole by terrorists in 2000. However, equipment was too expensive and bulky and the process of creating deliverables was too time consuming for this application to become commonplace.
Also, for many years there was no focused exposure by vendors of the technology to the forensic community. That changed in 2005 after the California Highway Patrol placed a million-dollar order for 3D scanners, software, and training for documenting major highway incidents. That large purchase triggered Leica’s U.S. western region salesperson, Tony Grissim, to focus on educating the broader forensic community about the benefits of 3D scanning for site and scene documentation.
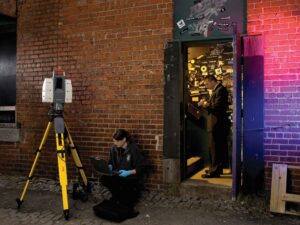
In 2008, laser scanning became a regular star in episodes of A&E Television’s Crime 360 show. Image credit: A&E
The timing of this initiative was coincident with a rash of new forensic and crime shows on television—each featuring advanced forensic technology and 3D animations. Grissim approached a couple of those TV shows with the idea of adding 3D laser scanning to their stories—and bingo!
In 2008, a 3D laser scanner and point cloud software became a staple on the new A&E TV show “Crime 360.” Later, the primetime NBC show, “Law & Order: Special Victims Unit,” showcased the technology in multiple episodes. Those shows helped trigger crime labs and other forensic departments to check out the technology and the snowball started rolling. Over time, forensics became a major new market for 3D laser scanning and the technology has delivered big benefits for countless cases over the years.
BIM/Construction – When 3D scanning first started, virtually no one had heard of BIM. Today, the use of 3D scanning for construction projects, especially in conjunction with BIM, may well be its largest single market.
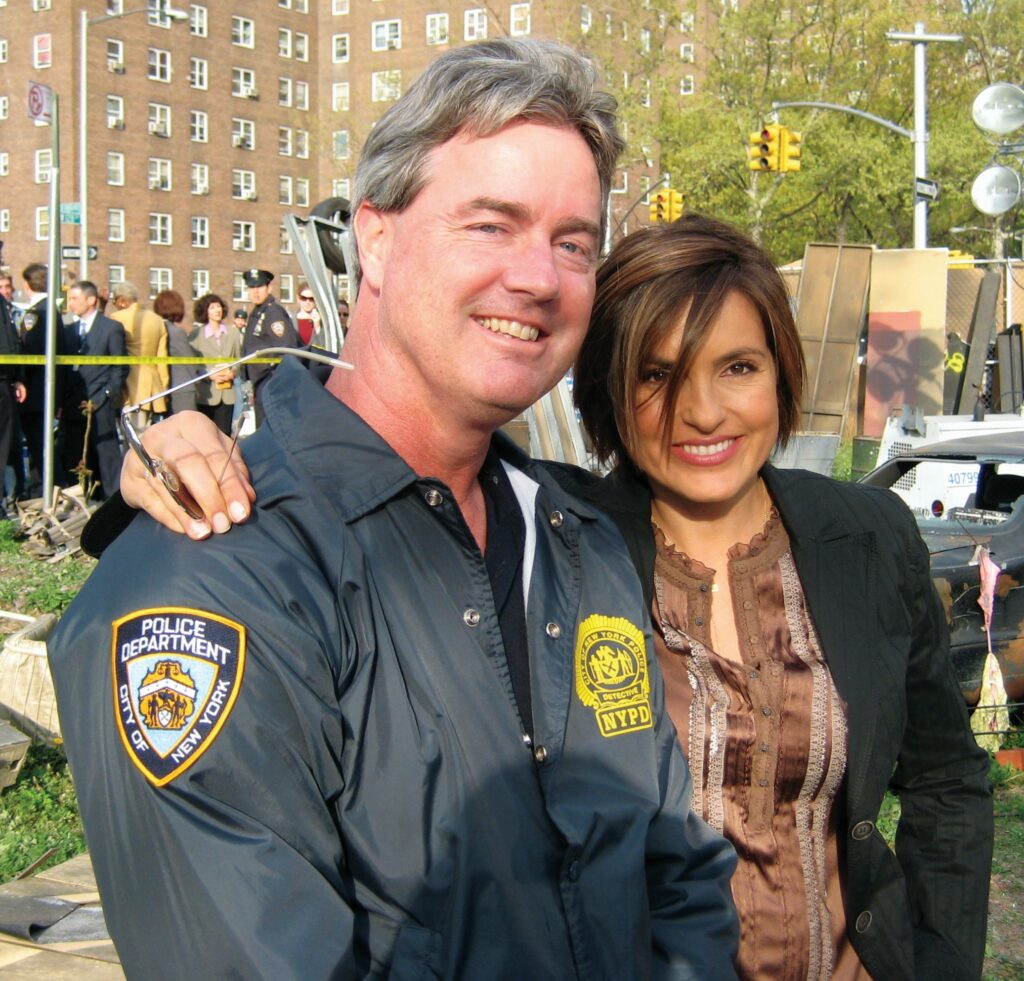
Leica’s Tony Grissim was first to focus on educating the forensics market about laser scanning. Here, Grissim is with Mariska Hargitay of NBC’s “Law and Order: Special Victim Unit” during a filming of a scene featuring a laser scanner. Credit: Tony Grissim
Two things drove a surge in demand for laser scanning in this segment. One was the sudden shift around 2012 of BIM being “nice to talk about” to being “must-have” in order to get a construction project award. The second driver was simply the dramatically improved cost-effectiveness and documented benefits of using 3D scanning for many construction applications, including QA/QC, retrofit design verification, progress monitoring, and construction coordination.
Marketing Residential Homes – As with many applications, the “potential” to use 3D laser scanning as a marketing aid, such as showing a site as it is today and then showing development plans for that site, was apparent. In the 2000s and through the global recession of 2008-2012, 3D scanning was often used to help market a survey or engineering company’s services.
However, none of that use of 3D scanning for marketing compares to the widespread use of it today for marketing residential homes. Matterport’s imaging scanner and process for transforming those scans and images into 3D walkthroughs of homes for sale has blown that market wide open. If
you go online to look at homes for sale you will see many listings that not only include Matterport’s 3D Walkthrough (and Matterport’s doll-house and floor-plan views) but also include Google’s StreetView of the home and street. Those StreetViews were also created using mobile scanning and imaging.
Other Major Advances
There have been still other major advances for the technology since the early days of 3D scanning. Here are my final picks.
Trimble & Topcon Entered the Market – While Leica Geosystems’ acquisition of Cyra Technologies in 2001 was a major milestone that helped legitimize the technology, Trimble’s entry in 2003 and Topcon’s entry in 2007 rounded out “the Big Three” survey instrument vendors to offer 3D scanning products, a huge further endorsement.
Industry Standards – For any new technology, the development of industry standards is an indicator of its successful adoption. Today there are numerous standards for 3D scanning and its related applications; however, the first big standards milestone in my view was the 2011 release of the ASTM E57 data format that enabled point cloud data from different types of scanners to be readily exchanged and used.
Advanced Users – In the beginning, 3D scanning was challenging to deploy, and many users stumbled. When a project didn’t go well, the technology often got a black eye. However, over time there emerged a group of advanced users whose skills not only showcased the power and value of 3D scanning but also showcased their own expertise. To those users, I tip my hat. You helped make the technology the great success that it is today.
Acknowledgments
Writing about the early days of 3D scanning from my personal perspective start-up days has been fun. Hopefully, readers have enjoyed these articles and been educated along the way. While much of what I wrote about came from my memory and various bits that I collected, I did additional research to check facts and fill out topics. Some research was online, but I also contacted numerous former colleagues and others for phone interviews or Zoom sessions. Many contacts provided invaluable insight as well as old documents and pictures. Here, I’m very happy to thank and acknowledge each of those individuals:
Ben Kacyra; Dr. Jerry Dimsdale; Dr. Johannes Riegl; Chris Korkalo; Greg Lawes; Dave Reinhart; Derrel Shaffer; Alan Lasky; Dr. Adam Spring; Keith Denton; Lewis Graham; Ron Aarts; Daniel Chudak; Tony Grissim; Frank Hahnel; Eric Sahlin
I would also like to thank xyHt for supporting this series in their highly-respected magazine. Finally, I would like to thank all of those who have provided such positive feedback to me on LinkedIn via links to the articles I’ve posted there. Being involved in the early days of 3D scanning was exciting. Writing about those days has been a blast.