A Norwegian company leverages Trimble technology to meet tight tolerances, high expectations and a frenetic pace
Sponsored Content
Tunnel surveys have typically been the domain of total stations run by multiple survey crews. For one tunnelling project in northern Norway, however, conventional technology was impeding survey crews’ speed and progress. One month into the project, those crews were replaced with one scanning total station operated by one surveyor. The technology switch has enabled her to manage two challenging tunnel environments and match the frenetic pace at six times the speed of multiple-person crews.
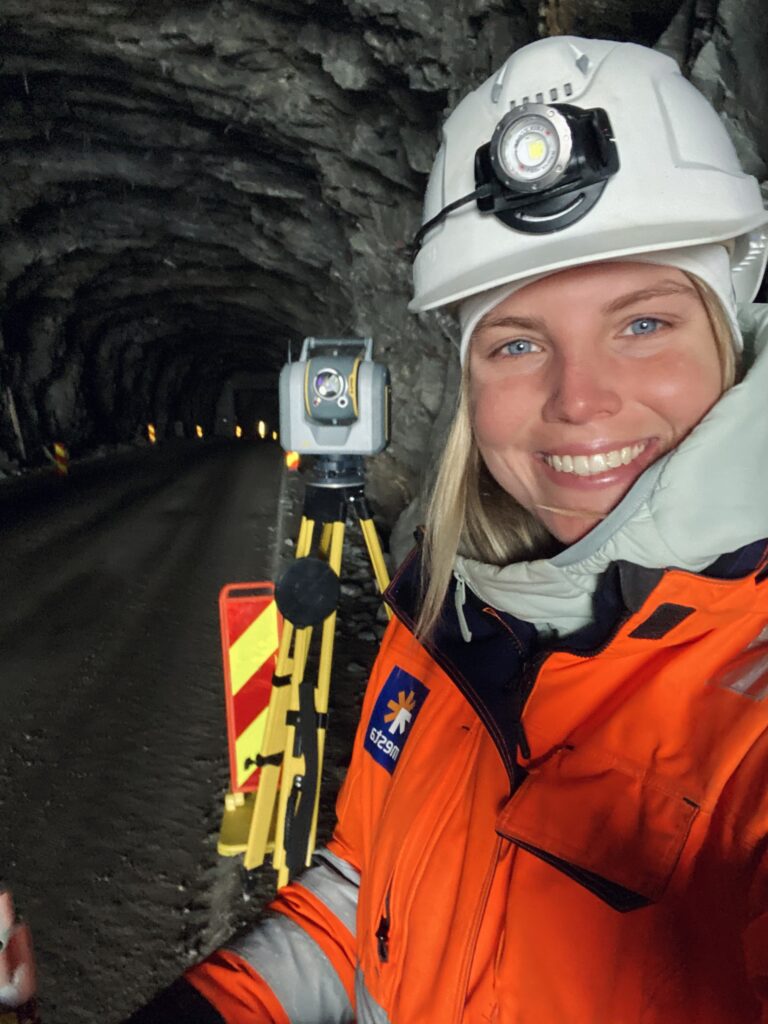
The Maursund and Kågen Tunnels are two critical passageways that connect the northern cities of Nordreisa on the mainland and Skjervøy on Kågen island. Built in 1991, both structures are undergoing extensive upgrades at a cost of NOK $211 million (US $24.8 million).
Mesta, a civil engineering construction company based in Lysaker, Norway, is responsible for the project. And Sylvia De Vuyst is the lone surveyor for both tunnels.
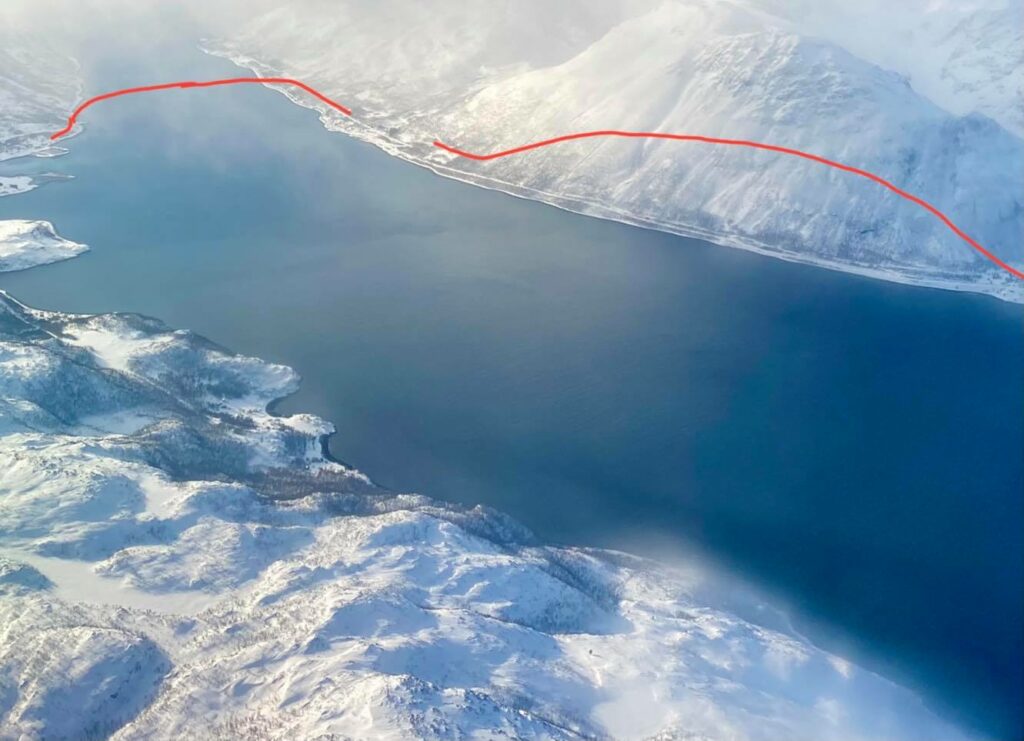
In addition to 24/7 traffic flow issues, there have been a multitude of complexities with the tunnels. Neither one has been designed with a pre-defined shape. Extracted rock is immediately reused by other firms so there are no stockpiles to measure for calculating volumes. And none of the machinery is equipped with machine control.
Given these challenges, De Vuyst needed technology that would be agile, efficient, reliable and precise. Based on extensive demos and previous experience with the Trimble SX10, Mesta chose the Trimble SX12 total station and scanner. Well suited for underground projects, it can scan a full dome at 100 m with a point density of 0.1 m in 11 minutes, and pinpoint a 3-mm diameter spot at 50 m with its green, eye-safe laser pointer.
“The combination of surveying and scanning technology makes it incredibly versatile––I can perform multiple functions from the same set up,” said De Vuyst. “It’s fast and precise which is important for such a dynamic environment. And its intuitive functionality and seamless workflow integration makes it easy to use and learn. I felt I would be in good hands with the SX12.”
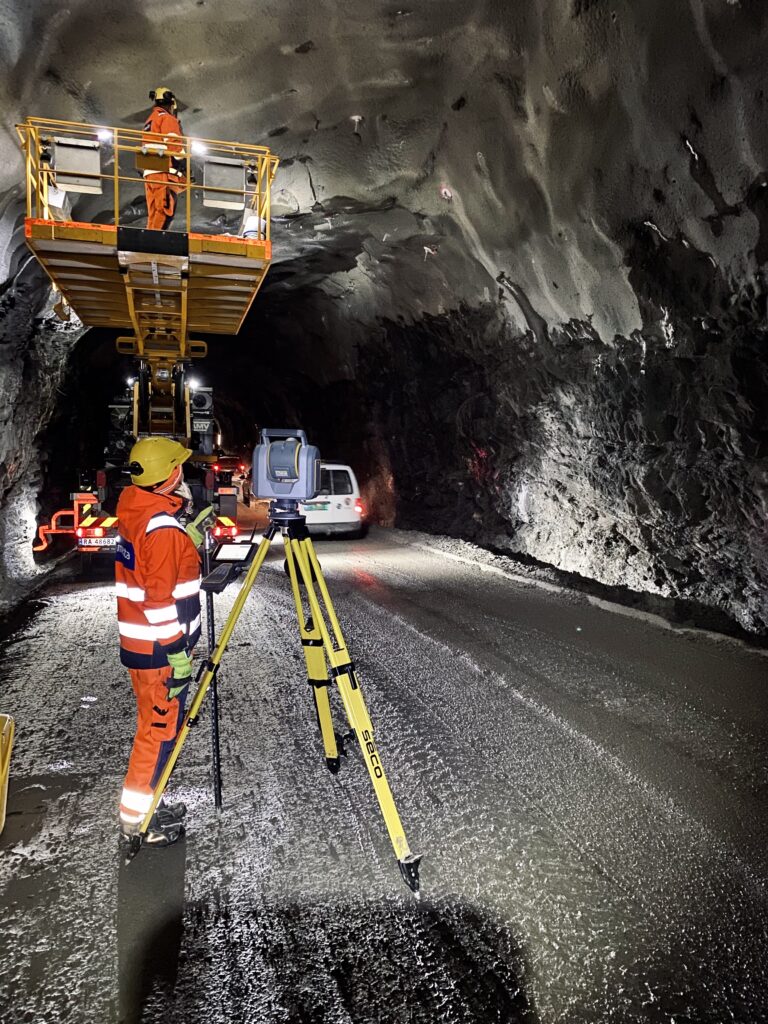
Volumes and bolts
Setting out prisms at 80-m intervals along the tunnel walls, De Vuyst has maintained a project control network accurate to 0.005 meters––the crucial foundation for setting out, calculating volumes and guiding the digging, blasting and drilling.
Since none of the excavators on site have machine control, De Vuyst has needed creativity for calculating volumes. She first created a 3D model of the Maursund’s “driving box”, the pre-defined height and width needed to allow vehicles to safely drive through. Scanning 60-m sections of the tunnel, she imported the 3D data into Trimble Business Center (TBC) to create a model of the road and then input the driving box dimensions to produce a linear 3D drawing of the box. She imported the drawing into Trimble Access Tunnels software and saved it on a Trimble TSC7 controller, enabling her to quickly check earthworks progress any time by measuring a point with the SX12 and comparing it to the driving box perimeter visible on the controller.
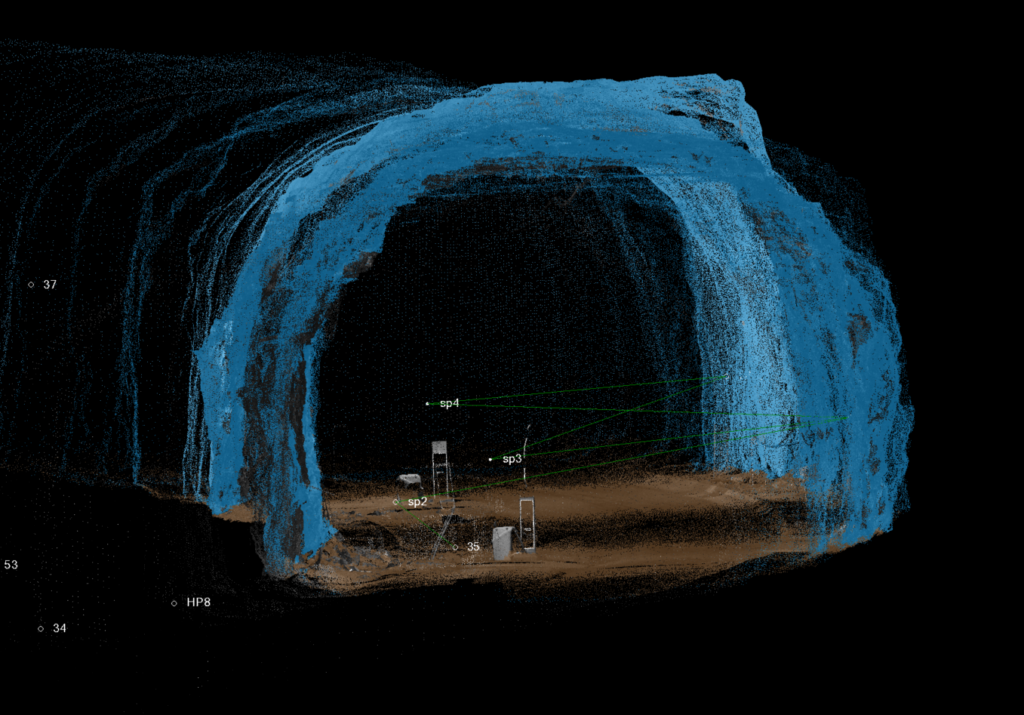
With TBC and its specialized Tunnel module, she also creates a tunnel shape, enabling her to combine survey controls with the density of points to calculate and verify earthwork volumes. Converting the 3D model to a tunnel profile drawing indicates precisely where more sediment needs to be removed and how much. Digger operators then use the prints in their cab as a machine control guide.
Tunnel profiles were particularly beneficial for positioning a technical building that needed to be constructed and assembled into a confined space with a tolerance of 0.5 m. Precision was paramount because the building’s pre-fabricated construction was designed to be within only a half-meter of the tunnel wall and the top of two of the building’s corners. De Vuyst used the SX12 to survey and calculate the excavation volumes to ensure the space was correct.
Setting out bolts for internal road signage has also been challenging, requiring De Vuyst to use the SX12’s green laser and a truck with a hydraulic bed. She determined and drew set-out lines indicating where the bolts should be placed and imported that 3D file into the TSC7’s software. Setting up the SX12 about 20 m from the truck, she used the set-out function and let the green laser navigate to the corresponding line. She then used the controller to move the laser along the line until it hit the precise break point. The person on the truck marked the tunnel ceiling at the exact bolt position.
“The clarity, precision and range of the green laser made the task so much easier,” said De Vuyst. “Even at 100 meters away, points are crystal clear.”
Follow Trimble:
Twitter: @TrimbleNews
Facebook: TrimbleSurvey
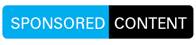