Above: The cramped field conditions in the underground tunnels are evident in this point cloud Trammel used to create the 3D tunnel piping.
From crowded boiler rooms to hard-to-reach underground tunnels, BIM experts tell us how following a smooth workflow is key to rapidly creating accurate 3D pipe models from point clouds.
Inside the Student Union Center building of the Central New Mexico (CNM) Community College in Albuquerque, New Mexico, Bob Ferguson was up for a new challenge that’s different from what he usually encounters in his daily job in the field. Within a short span of allotted class time, his task was to show students how to create an as-built 3D model of the building’s crammed boiler room.
Rapidly producing an accurate 3D model of pipes is hard work, especially if they twist and turn like noodles in unreachable corners. Thus, the boiler room was a good choice to display the capabilities of automated feature extraction, one of the latest technologies that has modernized the architecture, engineering and construction (AEC) industry in recent years.
Ferguson works as a scanning and virtual construction specialist for Jaynes Corporation, a full-service contractor with AEC projects in New Mexico, Colorado, and Texas. The company, which eagerly incorporated virtual construction technologies early on in its operations and has established an in-house scanning and modeling facility, encourages its employees to engage with local colleges by giving technology teach-ins to students in the communities where they operate, similar to the demonstration that Ferguson gave at CNM.
“I participate in community activities as often as I can, and I enjoy doing it,” he shared when asked why he took part in the demonstration at CNM.
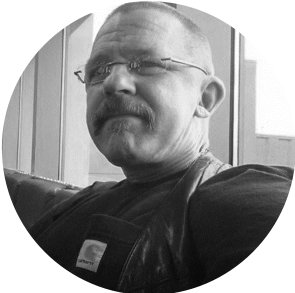
Bob Ferguson
On that day at the boiler room, Ferguson was wearing a teacher’s hat. The technology demonstration project at the architecture/engineering computer drafting program was an opportunity for the students, the future workforce of the AEC industry, to have a glimpse of the different stages required to create a building information model (BIM), starting from using 3D laser scanners for scanning the boiler room to using an automated extraction software for producing a 3D model of the pipes, valves, and other piping elements.
At the end of the activity, not only were the students able to participate in a real-life demonstration of the latest 3D modeling technology being used in the industry, but the registered scan and model were donated to the college’s drafting program which the students can use as future reference in their own projects.
Another beneficiary of the activity was the college facility manager who likewise received the up-to-date as-built model of the boiler room, which can be used in maintaining and possibly upgrading the equipment in the future.
“For me personally, there is no greater reward than the opportunity to share knowledge with students who are coming up through the trades,” Ferguson said. “As others have taught me, this is my chance to pay it back.”
According to him, the entire scanning, extraction, and modeling took less than 20 hours, a reduction of modeling time by about 75% compared to the more traditional workflow that students learn today.
How was he able to create the 3D pipe model of the boiler room in so little time?
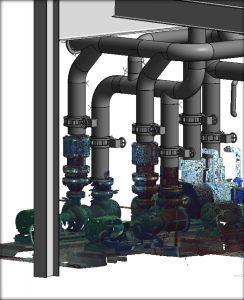
A portion of the 3D model from Ferguson’s project; the model was automatically extracted from a point cloud by EdgeWise and imported to Revit.
Seamless Pipe Modeling Workflow
Even if it were only a class demonstration, Ferguson worked with his team to show the students how professional BIM work is undertaken in the field. They followed a seamless workflow to accomplish the entire task, from laser scanning the room to creating the actual BIM.
“We wanted to demonstrate to the students a best-case scenario of exactly what the technology could accomplish,” Ferguson said.
From the start of the workflow process, Ferguson and his team set an extremely high level of modeling detail, a requirement that clients often ask for in real projects. “The resolution needed to be such that the bolt patterns on flanges of the boiler room could be identified and accurately measured,” described Ferguson.
To meet this demanding requirement, they used the FARO Focus S-150 laser scanner which was set to a resolution (1:4) that would capture about 44 million points in a single 360 degree scan and show details less than a quarter of an inch for objects 30 feet from the scanner. They also performed numerous scans, 21 in total, from multiple overlapping perspectives within the 4,000-square-foot boiler room. This is a large volume of data with very precise details.
After using the FARO Scene software to register the individual scans to create a single point cloud mode, Ferguson imported the data into EdgeWise, allowing him to automatically extract the architectural and piping elements of the boiler room. The structural objects were later obtained with EdgeWise’s user-guided semi-automatic extraction tools.
EdgeWise software, a product of the ClearEdge3D company from Virginia, uses computer vision algorithms that automatically extract geometry from point-cloud data. The feature-extraction algorithms and automated-modeling technology of EdgeWise can create walls, pipes, conduits, and steel beams from laser-scan point clouds.
The use of EdgeWise allows for shorter modeling time within a unified workflow from start-to-finish. In Ferguson’s demonstration, once the boiler room elements were extracted in EdgeWise, the final step was to export the model to Revit, Autodesk’s multidisciplinary BIM software. The software was also used to export the architectural elements to Revit as intelligent building components.
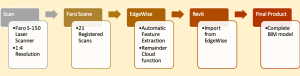
The workflow, from start-to-finish, that Ferguson followed to create the BIM of the CNM’s boiler room.
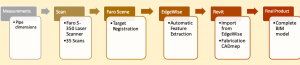
In this workflow, Trammell’s team first measured the pipe dimensions before scanning and creating the BIM of the hospital’s underground piping tunnels.
EdgeWise has a strong integration with Revit that allows it to transfer as-built models to Revit, which eliminates the need for manual modeling of pipes, conduit, and other elements in Revit, thus saving time and money. Ferguson estimated that had the project been attempted manually, the entire process would have required 80 hours, mostly to map, identify, and align each pipe run to the point cloud.
“EdgeWise saved us a tremendous amount of time [thanks to] the efficiency of the software and the technical support from ClearEdge3D,” said Ferguson.
Another time-saving EdgeWise function that Ferguson mentioned is the Remainder Cloud function. With it, modelers can extract, select, and isolate a single feature, such as a pipe, to create lightweight point clouds. By significantly decreasing the whole size of the project file, you can then quickly and easily measure the isolated pipe point cloud, trace its route from supply to boiler, and determine if it collides with other systems.
“The isolated point cloud greatly reduces the entire file size of the project, in turn, increasing the performance of the users authoring or viewing the model,” shares Ferguson. “This makes the modeling workflow faster and more efficient.”
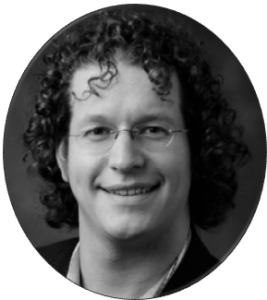
Kelly Cone
Kelly Cone, ClearEdge3D’s vice president of industry strategy, told us that their EdgeWise customers are reaping the advantages of current advances in computer vision technology.
“Computer vision technology gives our customers a massive head start on their as-built model. Our piping module, for instance, can usually extract 70 to 80% of the piping and auto-connect it into contiguous systems. So, if you’ve got 1,000 existing pipes (or conduit, or round duct) to model, wouldn’t you rather start your modeling with 750 of them already done for you with only a few hours of QA/QC to review them?” Kelly said.
ClearEdge3D was founded in 2006. The company’s track record of technological innovations in automated feature extraction, laser scanning, and 3D modeling space has been growing ever since they first released EdgeWise in 2009. The founders are recognized experts in the field of computer vision, hyperspectral data analysis, and lidar data analysis.
In 2018, Topcon acquired all the outstanding shares of ClearEdge3D. “It’s a great opportunity to combine the EdgeWise and Verity software platforms with the Topcon sales and financial resources to better serve all of our customers,” said its founder and CTO, Kevin Williams, in a press release.
Underground Pipe Modeling
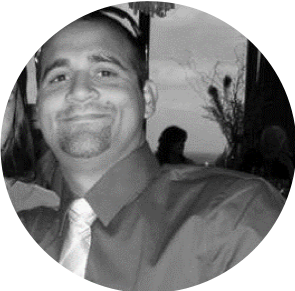
John Trammell
Another successful application of automated point cloud feature extraction in 3D pipe modeling was demonstrated by John Trammell, Brandt Company’s industrial virtual design manager. He had the same positive experience after using EdgeWise when the company was contracted to scan and create a 3D model of the underground pipes and structural steel in tight tunnels below a hospital in Texas.
Trammell and his team likewise followed a comparable modeling workflow to accomplish the tasks. Using a FARO Focus S-350 laser scanner, they captured 35 scans in the two dark underground tunnels, each of which measured about 6 feet wide and 350 feet long. And to make sure that the individual scans could be precisely registered into a single point cloud, the team performed target registration, ensuring that three or four targets were visible from each scan location. They also performed additional manual measurements of the pipe depth and diameter.
“We learned that spending time onsite to measure the thickness of the pipe insulation as well as pipe diameter ahead of the scanning saved a ton of time during the modeling process,” said Trammell.
The laser point clouds were then registered in FARO Scene before they were loaded into EdgeWise to automatically extract the underground pipes and model the valves, fittings and structural steel beams.
During EdgeWise’s automated pipe extraction process, the diameter, elevation, and slope of the piping systems are accurately identified. Then, the automatic connection tools in EdgeWise allowed the team to trace the underground piperuns even when they passed behind obstructions. “Sometimes real-world conditions don’t allow pipes to be hung in perfect 45- or 90-degree angles,” said Trammell. “EdgeWise lets you convert pipes with their real geometries—even if it’s an 88-degree turn.”
According to Trammell, the entire scanning and modeling process was completed in just under two weeks. But if the entire process were done manually, it would have taken eight weeks to deliver the work, reaching 80% of time saved. Trammell adds that the user interface of EdgeWise and its simplicity makes for a delightful user experience. “ClearEdge3D is allowing Brandt Companies to leverage construction technology in existing facilities in ways that have never been possible in the past,” he said.
Build Better Pipe Models
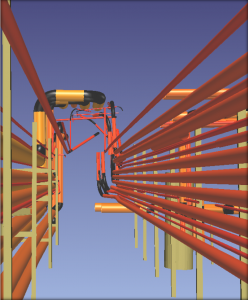
One of the underground piping segments in Trammell’s project, created using EdgeWise’s automated feature extraction technology.
Ferguson’s nine years of experience in virtual construction and scanning not only makes him a natural fit to conduct technology demonstrations in colleges; he is also an expert on process piping and scanning projects using BIM and virtual design and construction, with an AGC Certificate of Management-Building Information Modeling (CM-BIM) credential under his belt.
What pointers did he give the students after the demonstration? For Ferguson, who believes that every project has multiple challenges, his advice to them was “to always make sure that the derived as-built model meets the needs of the client.”
During the demonstration, Ferguson also recommended that they first answer these questions before starting any scanning and modeling project: • What are the scans being used for? • What elements do you need to see? • What is the level of detail needed? • What deliverables are expected? The following are Ferguson’s key takeaways for the students of CNM to prepare them in the future when it will be their turn to create their own 3D pipe models. Current BIM practitioners may heed them, too.
Ensure good coverage when scanning. The automated feature extraction algorithms of EdgeWise can work to its best ability when elements are scanned in the field from at least two opposing lines of sight.
According to Ferguson, doing this will “increase the coverage of the element by the laser, thus providing more points for the software to accurately interpret the geometry and extract the pipe elements faithfully.”
Understand your tools. For Ferguson, it is just as important to understand “what your tools cannot do as well as what they can do.” This will help with the expectations of your clients with regards to what they will be receiving as a deliverable, as well as help potential clients understand the capabilities of the technologies.
“Reality capture is just that, a snapshot of the exact existing conditions,” Ferguson shared. “Educating your clients that what they are going to receive will reflect ‘as exists’ conditions will help them greatly when adopting point clouds and the models derived from them into their workflow.”
Contact the creators of the tools you use and learn best practices from them. For Ferguson, there are almost as many reliable software options out there as there are people using them. But what separates the platforms from one another is the support offered by their technical staff and software engineers.
“Don’t hesitate to reach out to them,” he said. “You can almost be guaranteed that they have heard your question before and have if not one, multiple solutions. Yet the staff at ClearEdge3D have consistently responded in a timely manner and gone above and beyond to help me with any issue I have brought to the table.”
The Future Is with AI
According to a report published by Zion Market Research in 2018, the global BIM software and services market will be expected to grow in the coming years, reaching USD 10.36 billion by 2022. Authors of the report also predict that the growth in the BIM market is due to the improved visualization, the increased productivity, and the dramatic reduction in delivery time and costs with the use of BIM.
The time and cost savings can clearly be attributed to the use of automated feature extraction in the BIM process, thus making it commercially viable to turn large amounts of point-cloud data into usable 3D models. More businesses will adopt BIM when other opportunities open, such as fewer manual inputs required from users and, hopefully, lower-priced instruments.
What’s in store for customers in the future? Will we also see upcoming improvements in automated feature extraction technology? We asked again Kelly Cone of ClearEdge3D about what to expect with computer vision and how their products will evolve in the coming years.
“Computer vision, like all artificial intelligence-related fields, is seeing amazing benefits from developments in machine learning and the general advancement of processing power over time. So, approaches that were simply too computationally expensive or too complex before from a training perspective are now much more achievable,” Cone said.
Clearly, as the demand for BIM products continues to improve and grow, innovations in hardware will be required in order to meet the increasing computational demands of computer vision technologies. To overcome this limitation, Trammell, for example, used a dedicated computer solely for data processing due to the big file size of the point cloud in his hospital tunnel project. BIM operators make do with currently available hardware to create their as-built 3D models.
Cone believes in another couple of years we’ll see more sophisticated and accurate solutions due to the availability of more advanced AI approaches. “We will see an expansion in what we can realistically achieve with AI in terms of scope. Problems that might have been too complicated for more traditional methods might not be so difficult using machine learning.”
Another important issue is AI’s “black box” problem. Due to its nature, the use of automation creates a black box for the BIM user where data goes in the computer and then comes out as processed information. Whatever happens in between is not clear both to the user and the client. That is why Cone maintains that it is more interesting to approach AI as an interactive and assistive tool, with less “black box” and more “part of your team” structure, with clearer workflows.
“It is exciting for us to see these discussions on AI enter the mainstream over the last few years. The increased awareness we see in the AEC market will drive innovation and investment and that’s good for those of us already working to bring these kinds of solutions to this industry!” Cone shared.
And that is exactly what Ferguson is doing, bringing the technology to the mainstream through his participation in teaching demonstrations. He is clearly engaging with the industry’s future users, the students, and snowballing the awareness of BIM’s usefulness with the public. He hopes this will form a positive feedback loop that will encourage improvements in existing automated feature extraction software and services.
When asked if he will continue to give technology demonstrations in community colleges, Ferguson had this to say: “Being able to explain your workflow to others who have never been exposed or have little exposure to what you are doing actually helps me do my job better.”