An overview of a BIM solutions portfolio reveals the essential components for widespread implementation.
Are you tired of hearing about BIM yet? Get used to it.
The widespread adoption of BIM is quickly becoming an inevitability, with compelling drivers and essential tools already in place. In some economies, BIM has already been mandated for public works, and owners of large infrastructure portfolios are taking a more hands-on approach to managing projects and demanding the efficiencies that BIM can—and does—provide. Those who wish to stay competitive in this new paradigm for design and construction are driving BIM, as well.
But the biggest driver is all of us, we who, by extension, pay for any inefficiencies in constructing and operating everything that is built. For example, we all pay for cost overruns and schedule delays, though sadly we’ve become somewhat desensitized to the notion that every project will be late and over budget. What comes immediately to mind are big ticket public works, like transportation projects, but the same applies to commercial development, large medical facilities, industrial complexes, utilities, energy concerns—cost overruns are passed along to all of us in one way or another.
The construction industry still suffers from legacy inefficiencies. BIM promises to change that, and for early adopters it has yielded measurable gains. How practical is it to adopt BIM for even more projects?
If you have been following xyHt’s coverage of BIM—this will be an ongoing theme in 2019 and beyond—you’ll know that we’ve been examining various elements of modernized workflows. We will also be showing examples from the portfolios of solution providers: from GIS integration with design environments to constructioneering, continuous surveying, digital twins, and more.
During the 2018 Trimble Dimensions conference and exhibition, we took the opportunity to do a walk-though of Trimble’s entire BIM portfolio, or what the company calls “The Constructible Process.” The following is not an endorsement of any specific solutions, just a good example of the completeness of the toolboxes for BIM and how many of the solutions have been in place and broadly used for quite some time.
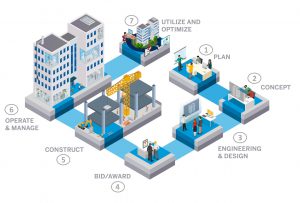
The lifecycle for infrastructure is often represented by seven general phases. In this illustration. key phases are numbered and you will find relevant sections with corresponding numbers.
Continuum
“It is the same for civil as for buildings,” said Mark Sawyer, Trimble’s director of industry strategy for construction, who walked us though the portfolio. “The thing we call the continuum is replicated on both sides of the business; for heavy civil and vertical construction there is the same lifecycle.
A project might begin with a master planner, or architectural service, or the owner doing a needs’ analysis,” Sawyer added. “Whether that is capital planning for a hospital group that may be spending hundreds of millions on new facilities, or a major transportation authority, or small capital planning for a one-off project—once the planning is done, this is where the owner can use products like e-Builder [owner-level project management cost/scheduling tool] and Manhattan [integrated workplace management system].”
The former is an owner-level project management cost/scheduling tool and the latter is an IWMS (integrated workplace management system). These can be implemented even before conceptual design has begun and throughout the entire life cycle. ①②③④⑤⑥⑦ (Unless otherwise stated, all of the solutions Sawyer mentions are Trimble products or from companies acquired by Trimble).
The concept phase ② that follows often happens before any pre-design surveying and mapping—the examination of conceptual alternatives often informs site selection.
“If it’s a really big project, there may be more than one [architecture firm] involved,” said Sawyer. “Usually, one is the design architect, doing the concepts ②, and others are production architects, cranking out the drawings ③ or working on a specialized scope of work.”
The concept phase is where familiar products are used, such as SketchUp, and focused solutions, like Sefaira, to do early-stage energy analysis ②③. With so much emphasis on the greening of buildings, the practicality and expected performance of various conceptual designs need to be known to the owners as early as possible.
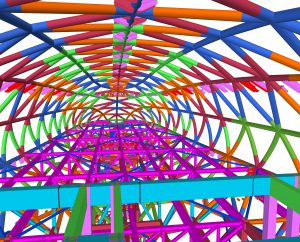
A structural model of the Museum of the Future (in UAE) received Tekla’s 2018 award for achievement in public projects. Source: Telka.
Conceptual Design
I have been using SketchUp for many years (including before it was acquired by Trimble), and I’m always amazed how much the SketchUp community has grown. We explored the beginnings of this boom in our Sept. 2012 feature, SketchUp..
There are now massive libraries of user-created objects and design tools by third-party developers. While it’s most definitely a tool for conceptual design, the richness of resources and capabilities brings SketchUp nearly to the level of a full-blown AEC design platform.
I asked Chris Dizon, who goes by the title of manager of customer success at Trimble (but who is also widely known by users in the SketchUp community), what is new in SketchUp for design and construction since I last used it a few years back.
“More than a few new functions. It has a lot to do with integration with other platforms,” said Dizon. “For instance, Tekla [Trimble’s suite for concrete and structural metal, see more below] now imports SketchUp directly and exports IFC models [BIM elements].”
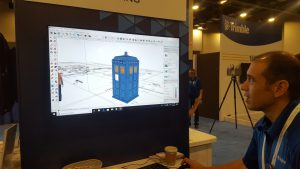
Chris Dizon demonstrates SketchUp at Trimble Dimensions 2018.
Dizon said, “What’s interesting—you know it from the conceptual day and people still use it for conceptual— is, thanks to our users that leverage the fact that SketchUp can be as detailed as anybody wants, people are actually getting detailed and using it for constructability later on in the process.” ②③④
I was shown an example from a general contractor (GC) who used an architectural model to communicate structural conflicts. It wasn’t super detailed—you don’t see every nut and bolt and you don’t see the MEP (mechanical, electrical, plumbing), although users also do those in SketchUp—but you can see the level of detail that the GC chooses. I can relate. I have seen different project teams get lost in a set of 2D design plans, even in 3D models in CAD programs, because viewing in those environments is not appropriate for people not used to navigating such detail.
We browsed through the online libraries of pre-engineered elements, furniture, landscape features, pre-fab walls, MEP components … the list of categories alone was pages long. Users, vendors, and suppliers continue to submit these ready-made 3D models daily. You could do a conceptual design of your next home or business in minutes just using those and third-party design tools. SketchUp is often used by folks wanting custom parts or structural elements; they can sometimes design it themselves and submit directly to fabricators. ②③④
We took a look at a building design that used a third-party tool for framing plans, added the criteria for spacing etc., applied this to a simple floorplan, and foomp! There was the framing in 3D. And when wall locations were changed, the plan adjusted dynamically. For grins I asked if I could drop Doctor Who’s TARDIS into the virtual living room, and we found more than a dozen full 3D models, no doubt created by fellow sci-fi aficionados.
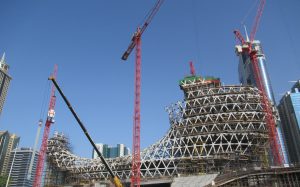
The Museum of the Future, under construction in the UAE. Source: Telka.
Visualization, Collaboration, Markup
Much is written about the visualization aspect of BIM, though some of the writing borders on hype when it’s about virtual reality and augmented reality (VR and AR), as those elements are still in progress. But the visualization power of the BIM collaboration hubs, like Trimble Connect, lies in its browser-based cloud viewer that allows team members, owners, and stakeholders to view and do simple markups where appropriate. These capabilities can be valuable in any phase of the lifecycle. ①②③④⑤⑥⑦
The subject of the current state of VR/AR and the potential to boost BIM would be fodder for a whole other series of articles, but let’s highlight a few developments.
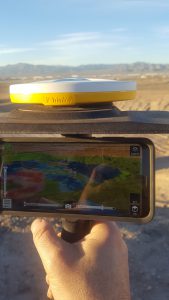
SiteVision aligns 3D construction models over the live view of a site. Orientation and positioning are achieved by integrating Catalyst and an attached antenna.
At the same conference at an offsite demonstration construction site, we got to try out the Trimble SiteVision system. A tablet is mounted on a handle, and you view the site though the tablet’s camera, but with the 3D proposed site-grading model superimposed over it. ⑤ This is functional but also cool to see in operation. A grader was reporting on its progress through the AR visualization: when the area shows green, they’ve reached grade.
The precise positioning and orientation are maintained with the internal MEMS sensors of the tablet and a Trimble Catalyst antenna mounted above the tablet, feeding processors on the tablet as a high precision GNSS receiver (see our January 2017 feature, “No Receiver Required), utilizing the Catalyst software-defined receiver service.
And on another level, mixed reality tools like the Microsoft HoloLens (see our 2015 feature, Blending Realities) are finding utility far beyond the gaming market, with substantial R&D for use in AEC applications. ②③④⑤⑥ In fact, the first application released for HoloLens was the Trimble SketchUp Viewer for HoloLens, and now there is Trimble Connect for HoloLens.
Sawyer said that mixed reality for BIM is “not just cool because it is cool. We are five years beyond that now.”
Things on the mixed reality front just got cooler with the announcement of the next-generation HoloLens (and the Trimble XR10, a version of the HoloLens 2 that is designed for AEC and fits on a hard hat). The announcement was at an AEC press pre-event we attended at the Mobile World Conference in Barcelona in February.
Never a Green Field
In every phase of the lifecycle ①②③④⑤⑥⑦ there can and will be contractors, subs, and design teams using tools and solutions that are not under the umbrella of a single solution provider.
Sawyer said, “We have never seen a greenfield project—not one—that has used only Trimble solutions. We have designed everything to be able to play well with whatever someone is using at any step of the way. The hub—the place where the data is from all of our solutions and the others for the GC, the owner, the subs, everyone involved—for us is Trimble Connect.”
“The hub—the place where the data is from all our solutions and the others for the GC, the owner, the subs—everyone involved—for us do not play nice together, they eventually might not get to play at all
Desktop, mobile, web: Trimble Connect, the kind of cloud-enabled collaborative environment we hear so much about when discussing BIM. There is no true BIM without some level of cloud collaboration.”
Emphasizing the cross-solution collaborative nature of Connect, Sawyer notes that when Trimble announced its release, design software firm Bentley announced connectivity to their ProjectWise service at the same time. This is an example of many such collaborations with firms like Autodesk, Esri, and others.
“Connect does not care if the data is from Bentley, Revit, Nemetschek, or other software,” said Sawyer. “It does not matter if it is a terrain model going to a Topcon or Leica system. Connect is the share point that provides the view and moves data back and forth.” ②③④⑤
“Design engineering, what architectural professionals call ‘design development’ [in American Institute of Architecture terminology] is going from schematic to more detailed design,” said Sawyer. “Once you have a site, for example, then you rough out underground design work, utilities, structural, mechanical, etc.”
And while the intense surveying and mapping may occur mostly in the pre-design phase ②, in a true BIM cycle—during the actual construction phase ⑤—there may also be a lot of what some call “continuous surveying “and other feedback fed into various systems to the mark progress, QA/QC, and check compliance. This is typically followed, after construction is complete, by final as-built surveys ⑤⑥.
Trimble Access on data controllers for total stations and GNSS rovers can import BIM elements, like IFC (Industry Foundation Classes standard) models for layout, and as-built surveys with additional paths of integrated data through TBC (survey office software) and through the Connect cloud hub. Things have progressed a long way since the days of ASCII point files, DXF, and handing over files on disks and thumb drives.
In most projects, much of the design ③, the production of construction contract drawings and models, would be performed in environments like Autodesk, Bentley, ARCHICAD, and others. Sawyer notes, though, that Trimble also offers a full civil -design suite called Novapoint that they acquired, and the from a successful Scandinavian engineering software development firm. The same group produces Quadri, a cloud-based collaboration tool for civil engineering design and construction. ③④
Award, Estimates, and Scheduling
“The award phase [④]: this is usually where heavy collaboration starts and where Connect kicks in,” said Sawyer. “[It’s] growing from collaboration in design teams, like with Autodesk BIM360 etc., and moving on to contractors who need to develop the constructability data. The team grows rapidly because you are now involving GCs and subs and all their estimators and schedulers.”
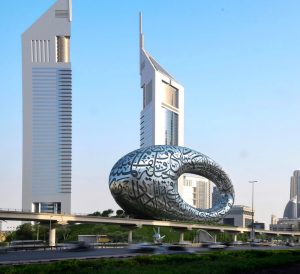
Artists rendering of the unique and structurally challenging new landmark in the UAE. Source: The Museum of the Future.
“Inside that you have, for example, mechanical contractors trying to figure out how much they will need to charge: electrical, survey, plumbing, and glass trying to come up with an estimate they can live with,” said Sawyer. “We have solutions to help each of those folks develop the level of construction models and data they need to make those estimates. They are going to move fast, and they need to react to multiple dynamic elements of the overall project design. Someone gets a price here and decides to alter the design over there.”
For estimating, their tools include Modelogix (a tool for GCs), WinEst (a general takeoff and estimating tool for construction), Tekla (for quantity takeoff of structural elements), Trimble Vico Office (developing scheduling from 3D models), and Accubid (for MEP estimating), to name a few. ④⑤There are discipline and project-type-specific packages as well for scheduling. For example, there’s Trimble TILOS for large linear, heavy civil projects. You can see the full array of these packages on their website.
Suffice it to say that Trimble and other solution providers for AEC have developed, or acquired, solutions for every step of the way, and a key takeaway is that no one has to (nor would be likely to) work completely under one proprietary umbrella. Various solutions can feed data into and draw data from collaborative BIM models and master project management systems.
“Things are bid differently in heavy civil than they are in vertical construction,” said Sawyer. “In heavy civil the contractor bids units of work, for example, by the cubic yard. If they are doing, say cut/fill for an underpass, and they find out the owner was off by 10%, then okay, it was by units. But in vertical construction, if a mechanical contractor bids for a whole system, like an HVAC or lift system, if something goes wrong, they may have to eat the difference. There are lot of differences in how you manage vertical and heavy civil projects, but for both, the better the data and tools you have, the better you can estimate, schedule, and track the work—lowering the risks.”
Constructability
④⑤ “BIM has typically been something you did in the office. But what really has value is building support for construction processes,” said Guy Erickson, business manager for Trimble’s Concrete Segment. “We like to focus on constructability. An example is concrete, forms, and rebar. If we are going to pour concrete, we need to know how to construct the forms and what steel needs to be in the concrete—down to that level of detail.” Of the many discipline-specific tools, we’re focusing on this one as an example.
I was given a tour inside Trimble’s Tekla Structures software, that automates many elements of developing those details, by Andy Dickey, global business development manager for that segment. “What we have done is make it easier to get from 2D to 3D or just work in 3D from the start, being able to bring in 2D docs like we traditionally do,” Dickey said. “We have developed tools and process that are a bit more intuitive, doing more with less people, faster, and being able to adjust on the fly to design changes.”
An additional value is to be able to create or add to 3D models, where dynamic, rules-based changes can happen. Dickey showed me how a complex rebar design changed live as he moved a wall in the model and how the concrete volumes updated.
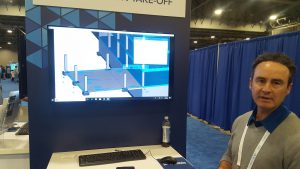
Guy Erickson demonstrates the Tekla Structures software at Dimensions 2018.
He said, “We want it to be buildable, not just conceptual. The benefits of a 3D model as you go downstream is that the layout will be easier; you can digest it through the cloud, on a tablet, and to other downstream discipline-specific apps and construction-management systems. The owner can feed back design changes, and the updates to our iron and concrete can be quick and painless.”
Telka can ingest and output IFC models, Revit models, SketchUp, and more. And some manufacturers of the big structural fabrication firms (e.g. CMC, Harris) can fabricate straight out of Tekla. IFC models can go into Trimble Field Link or other field software on a surveyor’s data controller for layout.
“We get data back from the field as-builts: Is our anchor in the right spot? How are our embeds and inserts?” said Dickey. “Traditional contractors, they want to ‘model it up’ so they bring in the PDFs or DWGs, and they will build the model from there. They are doing it because we made it easier to do. Tekla Structures has been doing steel detailing for 27 years and in concrete for 13 years.”
Today’s processing power is a major enabler for automation of detailing in models. ; the speed is impressive compared to the days when working in legacy rules-based engineering design software meant taking a long coffee break while an application would chug away.
“There were days when folks would have to wait many weeks for shop drawings,” said Dickey. “Today, we crank these out right away.”
“If you undergo a design change,” added Erickson, “say, we add another level of parking, all of that is automatically updated off the model. Make a change, cut a hole—it all changes dynamically.”
I asked them to cut a hole in the model on the screen—foomp! Everything updated. “This makes it much easier to look at constructable alternatives, going back again and again, refining, and advising the GC and owner with better informed options,” Erickson said.
Contract Phase
④⑤ “[Imagine that] I need to generate a ticket to send a crew out to service the chiller on the roof, or a survey crew to bring out a total station to lay out embeds in concrete, or a scanning total station to feed a point cloud back to see how it compares to the design model,” said Sawyer. “We have to have a way to manage that work, [track] what work needs to be accomplished each day, how much got done, what materials were moved and installed. Our customers must have a way to manage the submittal process, documentation, who gave that work order, which downstream teams need to be notified of progress. Mostly we want to make this all easier.”
“We have solutions like Prolog, a general contractor construction project-management solution for office and field, collaboration, cost control, purchasing, RFIs, submittals, daily reports, safety certificates,” said Sawyer. “Add in Vico, ProjectSight, e-Builder [see more about both below], and Viewpoint that span the construction lifecycle from planning, to product operations, to supply chain management, and then to project handover for the owner’s asset operations and maintenance.” The list of solutions would be too long to go over in detail in this article.
LEM
⑤ We’ve probably all had to manage the microcosm of a small project or site: our crew, gear, and materials. And in the past, you would have found success in managing through direct observations (or a priori knowledge) their whereabouts, condition, and progress. A firm grasp of the current state of Labor, Assets, and Materials (LEM) is essential to manage cost and schedule. But LEM management by the seat of one’s pants-—even for the most experienced and skilled project managers—will not cut it for large projects.
“In the world of heavy civil, knowing where the ‘big iron’ is, or has been, and for how long, lets you know what kind of work has been done,” said Sawyer. Referring to the tracking of heavy equipment: “I can track it with GPS and telemetry, know how many passes a compactor has made and where.”
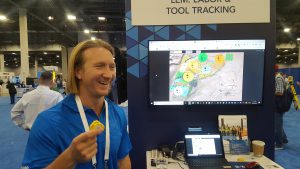
Matt Ramage shows one of the many types of small sensors used by these systems. LEM movements of the Dimensions offsite exhibit were tracked live at an exhibit booth miles away.
There are common tracking systems and applications for heavy civil, and these have been in broad use for many years, but when you’re managing vertical construction the focus is not so much on “big iron” (heavy equipment), but more on tracking those who do the work, the tools they use, and the materials they handle—those can indicate.
“In buildings, the equipment does not tell you much. It is the labor,” said Sawyer. “I know that if I had nine electricians on the second floor for x number of days, and I know how much progress has been done, then I can forecast the completion of future tasks—we track people and tools for vertical [construction].” The customer can put sensors on the tools and do badge control for workers; the more granular the sensor deployments, the better the data.
Systems for tracking tool and material locations and movements range from RFID chips to Bluetooth, to cellular, to conveyor systems’ metering of aggregates. Sawyer noted that Trimble, for instance, has the AllTrak cloud-based tool tracking solution, sensors like the GPS/cellular TAG200, and more.
But how to track labor? I was referred to Matthew Ramage, who has the title of worldwide marketing and new business segment director at Trimble but had also been hands-on with rolling out their automated labor and access tracking solution, CrewSight.
“A GC is interested in, or is required to, limit who gets on a site, so it can be a hard security measure. But [such a system] also serves other valuable types of tracking and compliance,” said Ramage. He was showing me a large, heavy turnstile on the exhibit floor of Trimble Dimensions that is activated by a badge reader. He said that turnstiles at sites are becoming commonplace, and, while heavy, they are as portable as other construction site facilities (they have forklift blade holes). There are many options for how to utilize these solutions; owners can choose what to focus on.
“At the most basic level, it does badge counting, acting like a dumb machine—but through the CrewSight system it automates time, attendance, health and safety, even drug-testing compliance” said Ramage. “What we have found for sites that do not have badge control, there might only be a check against records every few months or even only once a year. If you have a worker that is not up to date in safety, has not attended orientations, has failed drug tests, has had certifications or work permits expire before the next check—this opens up the GC to a lot of risk if something happens.”
Ramage said that access-control measures are big across Europe (where site-control requirements have traditionally been quite strict) and in other markets, with such systems now catching on in the U.S.
“Turnstiles is only one example,” said Ramage. “We have open-air readers for staff, tools, and equipment. For these needs, a precise position is not required—badges and tags are not GPS -enabled. But [the open-air readers can be used] for sites, areas of sites, activity zones, and warehouse locations. This is to gather activity metrics.”
I got to see a live example: the offsite demo area out in the desert, away from the main conference, was set up with CrewSight readers, and attendees, staff, tools, and equipment had badges and tags. Ramage showed me live views in CrewSight and AllTrak and records of my own badge from when I visited the site earlier that day. It might seem a bit “Big Brother,” but it can help solve some big problems for construction operations, compliance, safety, and scheduling.
Managing Billions in Spreadsheets?
“There are many cases where the owners of large-capital infrastructure portfolios—like some transportation authorities—who may be managing hundreds of millions, if not billions, of dollars of projects are doing so on spreadsheets,” said Chris Bell, VP for Trimble’s e-Builder division.
“We see this when we show up to help them to upgrade to systems that will give them a direct vision of what is going on in the processes, costs, and scheduling of the projects in their portfolios.” ①②③④⑤⑥
Probably the most shocking thing I learned while exploring the current state of capital projects was what I had heard rumor of but what Bell confirmed: billions of dollars managed on spreadsheets. This indicates that some owners and stakeholders were not actively involved in or aware of finer metrics of the projects. This can and does lead to bad decisions being made.
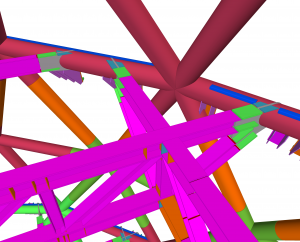
Due to the complexity of the Museum of the Future design, a dozen structural models were developed. Source: Tekla.
“The number-one cause for cost overruns and schedule delays is owner-directed changes,” ⑤ said Bell. “In many cases, the business analysis begins when the GC says the project is done, and the full impact of those changes is not known until then, and some post-project analysis is done.
“If we provide them with a system—e-Builder—that gives them a vision into the metrics that all of the other [BIM systems in the projects they have] and connects directly with their ERP [enterprise resource planning] and financial systems, then they can see if their proposed changes are causing self-inflicted wounds.
“What has happened over the past 10 years or so is that owners have merged their leadership and have chosen to take back a little bit of control in how capital projects get managed,” ①②③④⑤⑥⑦ said Bell. An example could be a transportation authority that plans to add x number of lane miles, with a capacity for x number of vehicles per hour at a desired cost of x dollars per unit. If the owner can see, in real-time, the impacts of change orders, costs, delays caused by lags in materials’ deliveries, weather delays, and more, then they can see how far they might be from meeting those original expectations and what corrective actions or compromises to consider.
This might sound like it could lead to owners micromanaging projects, but I believe that this instead creates a potential to boost efficiencies in other BIM systems—to push improvements in other workflow phases. Owners, GCs, and all involved will need more data, current, complete, and accurate—a further driver for broader BIM implementation.
Commissioning and Beyond
⑥⑦ Once construction is complete and the final inspections and as-built surveys are under way, the rich data of the BIM models, that had been so well managed and updated throughout this logical-labyrinth of processes and solutions, is now ready to hand over in the commissioning phase. The building or utility system, or highway, or facility goes live; people have moved in; and now you can use the same dataset to operate and manage it. (Expanding on those processes would be a whole new article.)
BIM—as nebulous as that term might seem—is going to happen; it is already happening. As we’ve seen with this cursory look at a portfolio of BIM solutions, the pieces are all in place. Its use is not going to be limited to mega-projects; the same efficiencies will be demanded by owners and stakeholders across the spectrum of projects. How well you fare in such an environment may depend on your a priori view of the entire work cycle; recognizing your role in it; and proactively adapting to master automation tools and adding value.