Clearpath Robotics CEO Matt Rendall discusses unmanned systems, land survey, and robotic industry trends.
The robot revolution is hitting a big milestone. Robotic use is expanding beyond research activities, aerial applications, and industrial manipulators through a new kind of deployment: the service robot. These robots are autonomous, they’re geospatially aware, and they can manipulate their surroundings. As a result, they have gained the attention of the biggest industries. One of the companies leading the charge is Kitchener, Ontario-based Clearpath Robotics, located in the tech supercluster of Toronto-Waterloo.

The active founders of Clearpath Robotics pose with a robotic utility vehicle (1 to r): Bryan Webb, Ryan Gariepy, and Matt Rendall.
Clearpath Robotics was started in 2009 by four mechatronics students from the University of Waterloo. They participated in a U.S. Army-funded competition to design a robot to detect and remove landmines. From this experience, the company’s flagship unmanned ground vehicle, the Husky, emerged. However, the founders soon realized the best market fit for their product was not the military but academics who wanted reliable unmanned vehicle platforms to hasten the speed of research.
Fast forward to today: Clearpath has added the Grizzly robotic utility vehicle and the compact Jackal to its fleet of autonomous ground vehicles. It offers the Kingfisher unmanned surface vessel for marine operations and others that are capable of navigating the land, sea, and air.
Now, the global robotics company is ramping up quickly to meet a large demand for its unmanned vehicles that automate the world’s dullest, dirtiest, and deadliest jobs. The leader at the helm is CEO and co-founder Matt Rendall. This is an opportune time to ask Rendall to reflect on how the unmanned robotics industry came to be, what land surveying with service robots looks like, and why he believes it’s time for non-aerial unmanned systems to shine.

Service robots like the Grizzly robotic utility vehicle can take specialized forms for different applications.
Land and Marine Drones Are Finally Here
Judging by the debates on privacy and FAA rulings, the focus of the public has been on unmanned aerial vehicles (UAV), but less on land and marine systems. Rendall believes there is a connection to the financial headstart given to unmanned aerial systems through military funding, which allowed the technology to mature faster.
“After [the terrorist attacks on] Sept 11th, [the U.S. military] poured tons of money into the [aerial] drone programs, and all of the defense contractors responded,” said the Waterloo-grad. “What that did was really great things in terms of validating the technology and making components and algorithms available for autonomous aerial systems.”
When the technology was ready to expand into civilian use, aerial survey was top of mind. “If you look at how expensive and challenging it is to get aerial survey conducting in various segments, it’s sort of the prime application for adoption of [UAV] after the military made it stable and cost-effective.”
Rendall explains that the military investment for land and marine systems has not been the same as for UAVs; thus, the transition into civilian applications, specifically land survey, has not been as fast. “There’s been aerial survey for a long time, way before drones,” he says. “It doesn’t mean there aren’t use-cases and requirements for land and marine survey.”
Rendall notes that the challenge for robotic land and marine survey technologies is that they did not receive the same benefit of heavy military investment to make them hardened and cost-effective. He points to the DARPA Grand Challenge, a prize competition for autonomous ground vehicles funded by the Defense Advanced Research Projects Agency, as an attempt to spur their development. “DARPA invested in the Grand Challenge to get driverless technology out, but they didn’t see it being ready for primetime as quickly as aerial systems.”
The second challenge, he says, is that there are more complications on ground from a safety perspective than there are in the air. “If you’re doing land survey, and there are people around, you need to be careful that you don’t hit them.”

Users can think beyond conventional bathymetry practices using unmanned surface vessels such as this Kingfisher.
Rendall acknowledges that airborne systems have their own challenges, but many of them have been worked out. “In air, you’re dealing with six degrees of freedom as opposed to three degrees of freedom” for land. However, he points out that autopilots have been around for a long time in commercial aviation, and they’re trusted for flight.
Despite Clearpath offering land, marine, and aerial systems, he acknowledges that the aerial drone market is a much more crowded space. “There are a lot more companies getting involved. Part of that is the testament to the maturity of the market and the demand for it, but also the continually decreasing barriers to entry. It’s becoming easier and easier to become a drone company and offer an aerial system.”
Rendall says that aerial drones are getting a ton of attention now, but over the next decade drones will quickly saturate their market. ”We’re going to see the proliferation of land-based and marine-based systems to help complement the aerial.”
UGV: Survey, Act, Repeat
Rendall wants people to imagine truly autonomous land vehicles differently, even beyond comparisons to driverless cars. “At a high level, they are the same concept,” he says. “Driverless cars are a really great reference point for the mainstream because Google and a number of other companies have done a lot to popularize the concept.”
But they’re not unmanned vehicles because they have passengers. “When you have people onboard, there are safety considerations and other factors that don’t come into play when you’re dealing with a truly unmanned autonomous vehicle.”
This means unmanned robots can take on very different, specialized forms for their application because the designs do not need to account for passenger factors such as comfort and safety. In Clearpath’s case, their unmanned systems serve industrial purposes. “The form factor [of UGVs, unmanned ground vehicles] can get much smaller. You can get into different kinetic configurations of vehicles for different motion profiles and different suspensions systems.”
For example, he mentions a pipeline survey where an unmanned vehicle is miniaturized to fit inside the pipeline, surveying inside and looking for damage.
The University of Chile’s Department of Electrical Engineering and the Advanced Mining Technology Center use an unmanned ground vehicle to perform surveys for underground and open-pit mining. They are researching automation technologies for resource extraction to find ways to minimize manpower in Chile’s dangerous mining environment. Because of the UGV’s open platform, radar, laser, and vision-based sensors could be installed and integrated together for 3D modeling. “The vehicle can take on very purpose-built form factors that becomes a tool in the toolkit of the land surveyor.”
According to Rendall, land-based robotic systems have a massive advantage over current work practices and aerial drones: autonomous land robots close the loop from survey to action because they can manipulate the environment. “People should start getting really excited about [this]. One thing that aerial drones can’t do [well] is act on their environment because they are so far above it.”
On construction sites, total stations, 3D scanners, and other measuring tools are used for layout and verification. In many cases, land-survey robots have the potential to eliminate these tools because they carry the same equipment. They are also geospatially aware via simultaneous location and mapping (SLAM) techniques, which localize them to a very high degree of precision. This knowledge can be combined with existing floorplans from the architects and construction management.
“Now, you have this ability to provide site support in a way you’ve never been able to do before,” Rendall explains. Such robots would have GPS, inertial, vision, and lidar sensors installed onboard. On top of that, they could be loaded with CAD or BIM (building information modeling) files. As a result, the autonomous vehicle can build a map, localize itself within it, reconcile the map that it developed against the a-priori BIM map, and orientate them on top of each other. “You can start doing change detection [by finding] the difference between the as-built and the drawing.”
Rendall says the biggest innovation is that the same robot can create changes on its surroundings before and during construction. It can perform highly accurate surveys but be equipped with a spray can or pinpoint tool and mark the four corners of a building or room to a very high degree of accuracy.
Apparently, this is the same as you would expect from a total-station user, but at a fraction of the time and with an operator that needs to much less skilled because the expert system is outsourced to the robot. “As soon as we start proving out those use cases, I think the adoption rate for land-based systems will exceed the adoption rate of aerial systems. The utility is so much more potent.”
He acknowledges that initially land systems had more challenges to overcome than other robotic systems. “You have more technical complexity on the ground.” A very small aerial drone weighing less than a pound can be made with parts from hobby components. “The problem on ground is you’re dealing with dirt, dust, and water and all kinds of different environmental factors.” he says. “Hobby-grade components just don’t cut it. You really don’t get the longevity on those hobby parts compared to when you deploy them for aerial application.”
From an engineering perspective, unmanned land vehicles need to be more rugged and have more industrial deployments. And there is more engineering upfront. Rendall says people cannot simply go online and purchase a drone kit for ground and then instrument it as easily as you can for aerial. For this reason, there is a higher starting cost associated with land survey drones.
In terms of GPS-denial and some of the technical challenges on ground, Rendall says there are ways around them with software. “If you’re dealing with GPS denial, then [traditionally] you need to have much higher-grade inertial. Then your costs go up.”
He explains the idea of sensor fusion and being able to take combined inputs from low-cost GPS, inertial, and vision sensors and fuse all the data together. “As you operate in a GPS-denied environment, the IMU and vision system are becoming the primary guidance systems, but when you get strong GPS connectivity, you can rely more on that.” He says the old barriers are quickly being overcome as such technologies mature, and it’s time for unmanned ground and marine vehicle to emerge.
Beyond Bathymetry: Unmanned Marine Vessels
The baseline application for Clearpath’s Kingfisher unmanned surface vessel (USV) is bathymetry. However, Rendall wants people to think beyond conventional bathymetric practices to extend the use of robotic systems that simply do underwater topography. “You have this intelligent robotic system that is surveying through a harbor, tailings pond, or whatever piece of water infrastructure of interest,” he says. “While it’s travelling and collecting bathymetric, what other pieces of data can complement the quantitative dataset for bathymetry?”
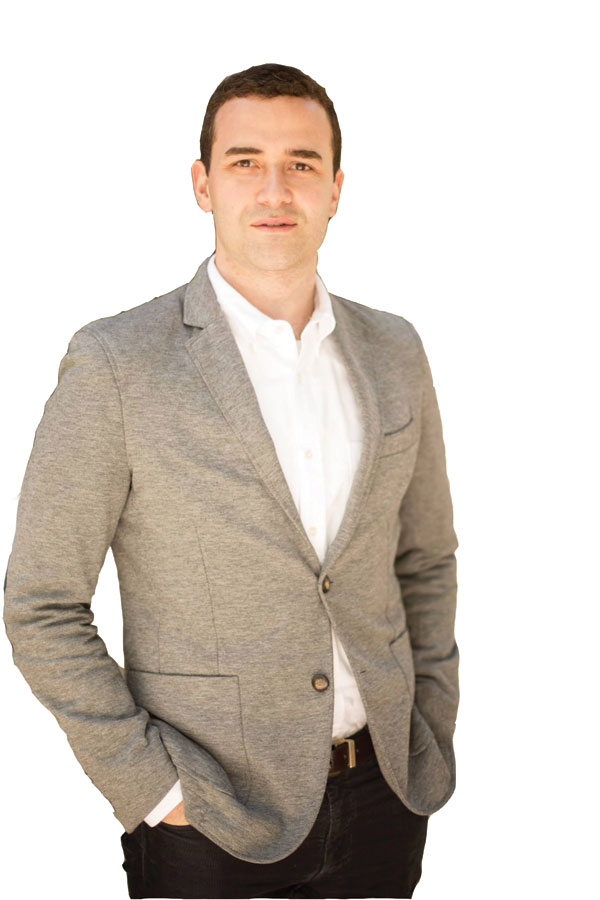
Matt Rendall, CEO of Clearpath Robotics, wants people to imagine autonomous land vehicles differently.
According to Rendall, there are many opportunities in water quality measurement correlated to very accurate bathymetric maps. Their customers are interested in dissolved oxygen content, torpidity, salinity, and temperature, along with the capture of thermocline information. A USV could automatically drop probes to determine where the thermocline is in a body of water, recover them, and trend the information over time.
“What’s interesting about marine systems is they are much similar in concept to [aerial] drones,” he says. The frequency with which surveys can be done increases because the barriers and costs decrease. In addition, there is less need for specialist-operators, so overall the friction associated with survey capture decreases. “These opportunities for trending and historical analysis [are] beyond what we’re currently able to do.”
Beyond hydrographic surveys, unmanned marine systems can be built to manipulate their environment. “We are very interested in dredging.” He explains that a bathymetric survey is conducted prior to the dredge, and the planners and water resource engineers create the dredging plan based on the topographical data.
“Dredging is not a highly precise discipline compared to survey,” he says. “You go in there with a boat or you dry dredge, and you dig out ground.” The dredging process is a black box, it’s very expensive, and the customer pays by volume removed. The underground area is re-surveyed and assessed if it is compliant with the plan.
“But what if you could survey every day?” asks Rendall. “What if you could do inline progress measurement to see how things are progressing against the plan? What if that gives you the insight to inline change your plan to cut days off your survey or cut dollars off your survey by refocusing where the dredge is happening and minimizing the amount of extraction necessary to accomplish the objective?”
Rendall explains that unmanned marine vessels complete the loop from survey to action, and dredging is a prime example where the ease of use, lowered cost, and increased frequency of bathymetric surveys provides the user with very tangible benefits compared to how things are currently being done.
Shift to Commercial Adoption
The robotic industry is transitioning from the realm of academia and military to commercial adoption and into mainstream use. Rendall reflects that the solution to a painful problem is driven by the industrial world but is experienced first in academia. Because most universities are led by industrial needs, this is where the innovation starts. “Clearpath started in the research market because we knew that’s where the industry was going to be born.”
Research and development are the first steps in the commercialization pipeline where the basic problems are researched to prove the viability of a concept. Then, specific applications are developed and continuously refined to validate use-cases. More iterations and validation occur to productize and take the concept to market, where there is need to support the product. Thus, the academic research into a solution may be a five- to ten-year horizon before commercialization.
Rendall acknowledges that product development is a pipeline, which means it works on a time dimension.
It’s apparent to Clearpath Robotics and Rendall that the entire autonomous vehicle industry is at the end of its academic timeline and ready to expand outward. Land- and marine-based unmanned systems are emerging from academia and into the hands of early adopters. “Hardware is mature enough such that fewer people are building their own hardware,” he says. “We’re in the stage of the market where people are building applications on top of someone else’s hardware and selling the value proposition of that application.”
Rendall cautions that the end markets do not care about unmanned systems. “It’s less about the robot and [its] novelty and more about what is the end result and output of that robot,” he says. ”The analogy that we use internally is that people will use drones until magic carpets are viable. It doesn’t matter what the technology is.”
People are fairly pragmatic about autonomous unmanned vehicles, he explains. They want to know how a robot can perform a dull, dangerous, and dirty task such that a human does not have to, at a price point that makes sense. It is evident that Clearpath Robotics and industrial service robots are ready to prove this to the world in the way they do best: by letting actions speak for themselves.
All photos courtesy of Clearpath Robotics.