An analysis of Autodesk’s software suite, BIM 360, reveals how BIM< can give project stakeholders unique access and insight across all phases of the AEC design process.
Large modern buildings are permeated with sensors and systems—plumbing, electrical, heating, cooling, ventilation, security, elevators, room scheduling, and, more and more often, even energy generation through wind turbines and solar panels. From earliest conception to demolition, efficient operations increasingly rely on building information modeling (BIM).
While the term has been around since the 1970s, BIM began to be commonly used about 15 years ago. A 2002 Autodesk white paper defined BIM as its “strategy for the application of information technology to the building industry,” and other software vendors also began to develop BIM products around that time. Autodesk BIM 360 is the company’s BIM software family for construction professionals, consisting of BIM 360 Glue, BIM 360 Layout, BIM 360 Docs, BIM 360 Field, BIM 360 Plan, and Building Ops.
Driving the Transformation to BIM
The mission of Autodesk’s AEC (architecture, engineering, and construction) team is “to drive the industry business transformation to BIM,” says Sarah Hodges, director of the company’s construction business line. Hodges, who has a degree in business administration and had her start in software working for the video industry, joined Autodesk’s AEC team about nine years ago.
Five or six years ago, Hodges recalls, her team was mostly focused on making people aware of what BIM is and the value it brings. Today, the conversation is mostly about adoption, because BIM has become “pervasive,” she says. This transformation is being driven not only by the software’s users, but also by certain governments and owners who are seeing its value.
Autodesk’s products include CAD, GIS, and BIM tools. “Over the years,” says Hodges, “we have begun to evolve our portfolio to enable these solutions and file formats to work together.”
BIM as a Process
Autodesk sees BIM as a process that enables buildings or infrastructure projects—roads, highways, bridges, utility projects—to be planned, designed, built, and managed. “We believe that BIM and the information that is at the core of that process is what enables the project’s stakeholders to have access and insight across all phases of the design process, through construction, even through operation,” says Hodges.
Architects were the first AEC segment to move to BIM. They and other professionals transitioned from their customary 2D drawings, 2D documentation, and 2D models to BIM as they realized that the latter increased their insight at all phases and enabled them to make earlier and more accurate decisions.
“From 2007 on, we started to see mechanical, electrical, plumbing, and structural engineers adopting BIM,” Hodges recalls. “Then, gradually, in the next three years or so, we started to see contractors also go to the table and realize the benefits.”
The contractors’ adoption of BIM coincided with the start of the economic recession in the United States, which many companies took as an opportunity to retool and update internal processes. Additionally, the General Services Administration in the United States and government agencies in Europe issued BIM mandates for government contracts, which also helped to spur the adoption of BIM.
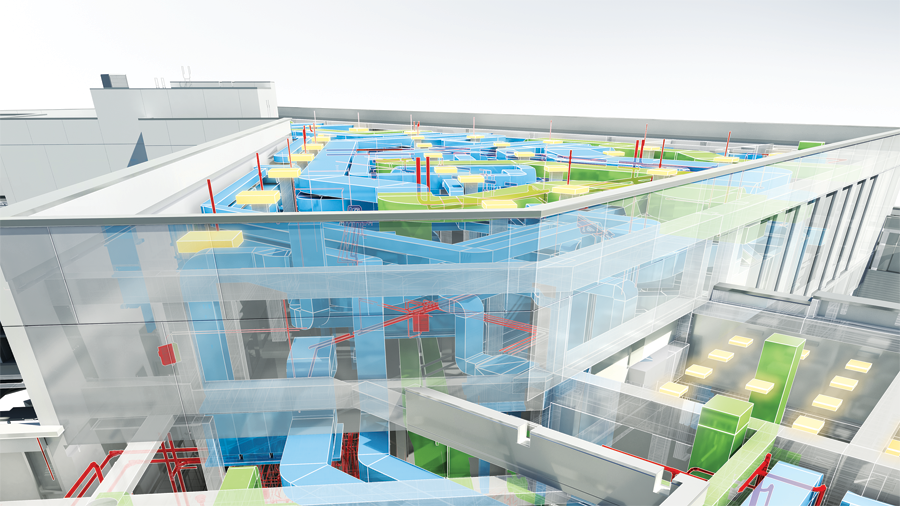
This model is of the St. Cloud Hospital addition and renovation, highlighting building systems and created using Autodesk’s Revit MEP, Revit Architecture, Revit Structure, and 3ds Max software products. Image courtesy of Dunham, Perkins+Will, MBJ, and St. Cloud Hospital.
BIM 360’s Components
A key concept underlying BIM 360 is shared data accessed via the cloud. The process starts with importing the design data, whether it is in a 3D model or 2D design information.
In the very earliest phases of a construction project, BIM 360 Glue facilitates the hand-off from design to construction by making visible any “clashes,” such as pipes running through structural members, so that they can be resolved before construction begins. This can avoid thousands of dollars of rework in the field after components have already been installed.
BIM 360 Layout can then connect BIM to total stations that indicate precise locations for installations, such as where hangers might go for piping or where walls might be put into place.
“What formerly required many people on a team and multiple shop drawings being sent all over the place now can be done at millimeter accuracy by one person with a total station,” says Peter Billante, Autodesk’s vice president of product management and marketing.
Layout enables users to verify during construction that installations were done in the right place. BIM 360 Field is designed to manage the QA/QC safety and commissioning processes.
“A typical construction project includes thousands of installations, many of them triggered by different checklists,” Billante explains. “BIM 360 Field lets you bring those out to the field on a mobile device, relate them back to designs, capture issues and tasks for follow-up and so forth, report those out, and understand how your project is performing.”
BIM 360 Plan, which was added last year, handles construction scheduling two to four weeks ahead and enables “lean” scheduling. For example, it will display when inventory is coming in for one trade at the same time that another trade needs to work in the same area and enable users to make adjustments.
BIM 360 Docs, which Autodesk recently launched, “emerged out of the need to have fast and easy access into project design information,” says Billante. Unlike Glue, which deals with 3D models, Docs accepts any kind of design information.
A big problem with construction is re-work, often due to that fact that people on the job site don’t have the most up-to-date designs. “Let’s say that you are 23 stories up and need to go back to the job trailer or the office to look up an answer to a question from the electrical sub: that’s a 20-minute round trip,” says Billante. “If you add it up over the schedule of a typical construction project for 22 months, that time savings per person really does affect the efficiency and the productivity of the project.” Docs addresses that problem by giving everyone on the team access to up-to-date design information via mobile devices.
The Shanghai Tower Project
Rendering of the recently completed Shanghai Tower. Image courtesy of Shanghai Tower Construction and Development Co., Ltd. Rendering by Gensler.
BIM enables different design disciplines to work together in a single platform and to perform building analysis and simulation far earlier in the design process than was previously possible. This is particularly important to improve sustainability.
An example is the 128-story Shanghai Tower, the world’s second-tallest building, in Lujiazui, Pudong, Shanghai, which Autodesk helped to design and build. It was designed to have a transparent skin that creates some natural ventilation. This helps conserve the tower’s energy and moderate its temperature.
“Much of that skin would not have been possible if the teams hadn’t used BIM to go through some very early green building analysis,” says Sarah Hodges, director of Autodesk’s construction business line. “They used our product, Revit, to look at different scenarios and analyze different patterns—such as where the sun was at various points during the day, how much heat was being transferred to the building, and what natural heating and cooling was happening in the building.
“They were able to use the feedback from their BIM process to understand the energy performance and then share that information not only with the engineers, the consultants, and the contractors on the building project, but also with the owner, who was inspired to make sure that this was a sustainable project and to make better decisions.”
BIM was also a key to designing the tower’s striking rotating angle façade to best withstand high winds and earthquakes; to use significantly less material than could have been done through a different process; and to help reduce its energy consumption once it was fully occupied, says Hodges.
Hodges adds, “Autodesk Insight 360 is the next evolution of sustainable design or building energy analysis that we are bringing to the market. It connects not only with Revit but also with FormIt 360, which is used for conceptual design.” Insight 360 also integrates various standards for building heating, cooling and lighting and produces visualizations that can be shared not only with the design team but also with the owners or other stakeholders who lack a technical background but need visual insight into how their building is going to perform.
How BIM Is Changing Planning and Design
BIM’s ability to detect clashes between different design elements is one of the ways in which it is changing building planning and design. Structural, architectural, mechanical, electrical, and plumbing designers, Billante recalls, used to meet weekly to compare and discuss their designs, report on problems they had solved, and uncover new ones—resulting in weeks of design iterations. Now, by putting their designs in the cloud, team members can immediately see the impact of their changes and address problems.
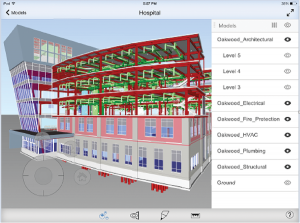
This model was created using Autodesk BIM 360 Glue, a cloud-based BIM management and collaboration product that helps users review projects and resolve coordination issues. Image courtesy of Autodesk.
Another important way in which BIM is changing building management is that, throughout the course of a project, it is creating a database of information about it, which becomes a significant asset when turning the building over to its owner.
Before BIM, owners would receive several bankers’ boxes and maybe a DVD listing all the documents. “Now,” says Billante, “what we really have is a virtual asset that can be handed over to the owner. If you are implementing, say, an operations system, it automatically populates it to begin your facilities maintenance and provide those maintenance cycles right away. That is something that has never been done before. It is reducing your risk as a building owner on your start-up.”
Blurring the Lines between GIS and BIM
Just as the lines between CAD and BIM have become increasingly blurred, so have those between GIS and BIM. “GIS data continues to be extremely important to our customers’ workflows and to the industry that we serve,” says Hodges. “We believe that GIS data is part of the BIM process, so we have to make sure that it finds a way into the new world among our BIM workflows that our customers are using.”
GIS data is essential to making informed decisions about the exact location of a building. InfraWorks 360, Autodesk’s GIS modeling platform, “brings CAD and GIS data into a modeling environment and allows our customers to optimize not only their designs but also the construction phase,” Hodges explains. “It also allows the information to live on through the life of the asset, which becomes increasingly valuable for the operations and maintenance phase.”
While today BIM 360 is used mostly for vertical construction, Autodesk is looking to extend some of its workflows into horizontal assets, such as roads and even utilities.
The Role of Sensors
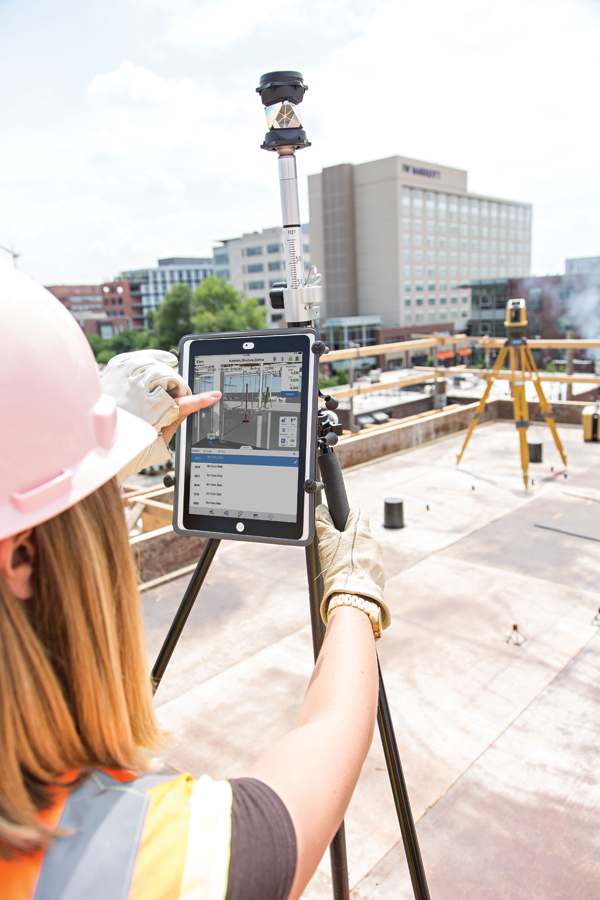
The BIM 360 Layout app is on an iPad connected to a Topcon LN-100 robotic instrument, guiding the user to physical locations on the job site. Image courtesy of PCL Construction.
The Internet of Things, based on different kinds of sensors, is exploding. Rather than design BIM 360 to be used with an individual set of sensors, Autodesk has enabled it to connect to many different types of sensors, via APIs (application program interfaces). “One of the benefits that you get from being a cloud-based solution is that we can publish those APIs—at this point, many of them have been around for years and are pretty mature—and our partners and customers can build solutions on top of them that take advantage of our sensor information,” says Billante.
Several Autodesk partner companies make devices that take advantage of BIM 360’s API. DAQRI makes a location-aware, augmented reality, construction hard hat that senses such things as temperature and dust and gives visual feedback to the user. Redpoint Positioning makes sensors that can be placed inside buildings to create interior positioning systems, to an accuracy of 20 cm. Panoramic Power makes a post-handover solution that connects a building model to sensors that detect pieces of electrical equipment, such as air handlers or chillers, through the electrical system and proactively monitors them through voltage changes to detect problems. It then sends notifications to Autodesk Building Ops, a building maintenance system, to preventatively act on those problems before they cause an outage.
BIM 360 Layout also features integration to total stations. “It works today with total stations from Topcon and Leica, which have been tightly involved with the evolution of that product over time,” says Billante. “It has an iPad application that connects into those devices so that you get visual feedback directly there on the job site about where you are within the model and can interact with different workflows.”